Uyda guruchni qanday pishirish kerak. Guruch va uning xususiyatlari. Sovuq ishlov berish: mis, qo'rg'oshin va alyuminiy
Mis va uning qotishmalarini issiqlik bilan ishlov berish texnologiyasini ishlab chiqishda ularning ikkita xususiyatini hisobga olish kerak: yuqori issiqlik o'tkazuvchanligi va isitish vaqtida gazlar bilan faol o'zaro ta'sir. Yupqa mahsulotlar va yarim tayyor mahsulotlarni isitishda issiqlik o'tkazuvchanligi ikkinchi darajali ahamiyatga ega. Massiv mahsulotlarni qizdirganda, misning yuqori issiqlik o'tkazuvchanligi, masalan, titanium qotishmalari bilan solishtirganda, butun tasavvurlar bo'ylab tezroq va bir tekis qizdirilishining sababidir.Yuqori issiqlik o'tkazuvchanligi tufayli mis qotishmalarini mustahkamlovchi issiqlik bilan ishlov berish jarayonida qattiqlashuv muammosi paydo bo'lmaydi. Amalda qo'llaniladigan yarim tayyor mahsulotlar va mahsulotlarning o'lchamlari bilan ular kaltsiylanadi.
Mis va unga asoslangan qotishmalar kislorod va suv bug'lari bilan faol o'zaro ta'sirlashganda ko'tarilgan haroratlar, alyuminiy va uning qotishmalariga qaraganda kamida ko'proq intensiv ravishda, bu xususiyat bilan bog'liq holda, mis va uning qotishmalaridan tayyorlangan yarim tayyor mahsulotlar va mahsulotlarni issiqlik bilan ishlov berish jarayonida, texnologiyada ko'pincha himoya atmosferalari qo'llaniladi. issiqlik bilan ishlov berish Alyuminiyni himoya qiluvchi atmosferalar kam uchraydi.
Mis va uning qotishmalarini tavlash qotib qolish jarayonida yoki mexanik ta'sir yoki oldingi issiqlik bilan ishlov berish natijasida yuzaga kelgan muvozanat tuzilmasidan og'ishlarni bartaraf etish uchun amalga oshiriladi.
Gomogenizatsiya tavlanishi qotishmalarning tarkibiy qismlarining erishiga olib kelmasdan, ingotlarni mumkin bo'lgan eng yuqori haroratga qizdirishni o'z ichiga oladi. Mis va guruchlarda likvidlanish hodisalari ahamiyatsiz rivojlanadi va ularni bir hil holga keltirish uchun ingotlarni issiq bosim bilan ishlov berish uchun qizdirish kifoya qiladi.
Gomogenizatsiya tavlanishini talab qiladigan asosiy mis qotishmalari qalay bronzalaridir, chunki Cu-Sn tizimidagi suyuq va qattiq fazalarning tarkibi juda farq qiladi va shuning uchun intensiv dendritik suyuqlik rivojlanadi.
Gomogenizatsiya tavlanishi natijasida ingotlarning tuzilishi va kimyoviy tarkibining bir xilligi ortadi. Gomogenizatsiya tavlanishi yuqori sifatli yakuniy mahsulotni olish shartlaridan biridir.
Qayta kristallanish bilan tavlanish mis va uning asosidagi yarim tayyor qotishmalarni ishlab chiqarishda keng tarqalgan texnologik bosqichlardan biridir.
Misning qayta kristallanishi boshlangan harorat Zr, Cd, Sn, Sb, Cr ga intensiv ravishda oshadi, Ni, Zn, Fe, Co esa kuchsiz ta'sir qiladi. Bir vaqtning o'zida bir nechta elementlarning mavjudligida qayta kristallanishning boshlanishi haroratining oshishi qo'shimcha emas, lekin eng samarali ta'sir qiluvchi nopoklik hissasidan biroz oshadi. Ba'zi hollarda, masalan, qo'rg'oshin va oltingugurt misga kiritilganda, umumiy ta'sir individual ta'sirlardan yuqori bo'ladi. Fosfor bilan deoksidlangan mis, kislorod o'z ichiga olgan misdan farqli o'laroq, tavlanish paytida kuchli don o'sishiga moyil bo'ladi, fosfor borligida qayta kristallanish chegarasi yuqori haroratga o'tadi.
800 ° C da 6 soat davomida tavlangandan keyin 2 * 10v-2 sm gacha bo'lgan don o'lchamiga ega kislorodsiz mis uchun kritik deformatsiya darajasi taxminan 1% ni tashkil qiladi. Temir kabi aralashmalar deformatsiyaning tanqidiy darajasini oshiradi, bu guruch uchun 5-12% ni tashkil qiladi (44-rasm).
Guruchning qayta kristallanish haroratiga oldingi ishlov berish, birinchi navbatda, sovuq deformatsiya darajasi va ushbu qayta ishlash jarayonida hosil bo'lgan donning kattaligi ham ta'sir qiladi. Misol uchun, L95 guruchining 440 ° C haroratda qayta kristallanishi boshlanishidan oldingi vaqt 30% sovuq deformatsiya darajasida 30 minut va 80% deformatsiya darajasida 1 minut.
Dastlabki donning kattaligi kristallanish jarayoniga deformatsiya darajasining oshishiga teskari ta'sir qiladi. Misol uchun, 30 va 15 mkm bo'lgan boshlang'ich don o'lchamiga ega bo'lgan L95 qotishmasida 440 ° C haroratda 50% deformatsiyadan keyin tavlanish mos ravishda 5 va 1 daqiqadan so'ng qayta kristallanishga olib keladi. Shu bilan birga, agar tavlanish harorati 140 ° C dan oshsa, dastlabki donning o'lchami qayta kristallanish tezligiga ta'sir qilmaydi.
Shaklda. 45-rasmda a-guruchlar tarkibining tavlanish haroratiga ta'siri to'g'risidagi ma'lumotlar ko'rsatilgan (deformatsiya darajasi 45%, tavlanish vaqti 30 min), bu berilgan don hajmini olishni ta'minlaydi. Deformatsiya va tavlanishning bir xil sharoitlarida rux miqdori ortib borishi bilan don hajmi kamayadi, minimal darajaga etadi va keyin ortadi. Shunday qilib, masalan, 500 ° C da 30 daqiqa davomida tavlangandan so'ng, don hajmi: misda 0,025 mm; guruchda 15% Zn 0,015 mm, guruchda 35% Zn 0,035 mm. 45-rasmda ham a-brasslarda don nisbatan o'sishni boshlaganini ko'rsatadi past haroratlar va solidus haroratigacha o'sadi, ikki fazali (a+b)- va maxsus guruchlarda don o'sishi, qoida tariqasida, faqat bitta b-faza qoladigan haroratlarda sodir bo'ladi. Masalan, L59 guruch uchun donning sezilarli o'sishi 750 ° C dan yuqori haroratda yumshatilganda boshlanadi.
Guruchning tavlanish harorati qayta kristallanish boshlanadigan haroratdan taxminan 250-350 ° S yuqori tanlanadi (16-jadval).
Tarkibida 32-39% Zn boʻlgan mis qotishmalari a⇔a+b oʻtishdan yuqori haroratlarda tavlanganda, donning notekis oʻsishiga sabab boʻladigan b faza ajralib chiqadi. Bunday qotishmalarni Cu-Zn tizimining a⇔a+b muvozanat chizig'idan oshmaydigan haroratlarda tavlash maqsadga muvofiqdir. Shu munosabat bilan, mis tarkibidagi ruxning maksimal eruvchanligi nuqtasiga yaqin bo'lgan guruch haroratni nazorat qilishning yuqori aniqligi va misning butun hajmi bo'ylab taqsimlanishining yuqori bir xilligi bilan pechlarda tavlanishi kerak.
Shaklda. 46 mahalliy va jahon amaliyotida to'plangan texnologik tavsiyalarni umumlashtirish natijalariga ko'ra oddiy guruchlar uchun optimal tavlanish rejimlarini ko'rsatadi. Rux miqdori ortishi bilan guruchning to'liq tavlanish harorati ortishi tendentsiyasi mavjud.
Guruchlar uchun qayta kristallanishni yumshatish usullarini tanlashda, a/a+b faza chegarasiga yaqin joylashgan qotishmalar (46-rasm) misda sinkning o'zgaruvchan eruvchanligi tufayli termik mustahkamlanishi mumkinligini hisobga olish kerak. Tarkibida 34% dan ortiq Zn boʻlgan guruchlarning qattiqlashishi ularni qarishga moyil qiladi (47-rasm), rux miqdori 42% gacha oshishi bilan qarish jarayonida qotib qolish qobiliyati ortadi. Amaliy dastur Men guruchning bunday termal qotib qolishini topmadim. Shunga qaramay, qayta kristallanish tavlanishidan keyin L63 tipidagi guruchlarning sovutish tezligi ularning mexanik xususiyatlariga ta'sir qiladi. 34% dan ortiq Zn ni o'z ichiga olgan a-guruchlarda va a+b-guruchlarda o'ta to'yingan eritmalarning parchalanish ehtimoli ham stressni kamaytirish uchun tavlanish rejimlarini tanlashda hisobga olinishi kerak. Qattiq sovuq deformatsiyalar tavlanish paytida o'ta to'yingan a- va b-eritmalarning parchalanishini tezlashtirishi mumkin.
Adabiyot ma'lumotlariga ko'ra, L63 guruchning qayta kristallanishi boshlanadigan harorat 250 dan 480 ° C gacha. L63 qotishmasidagi eng nozik taneli struktura 300-400 ° S haroratda tavlanishdan keyin hosil bo'ladi. Oldingi daraja qanchalik yuqori bo'lsa. sovuq deformatsiya, bir xil tavlanish sharoitida qayta kristallangan donning hajmi qanchalik kichik bo'lsa va qattiqlik katta bo'ladi (48-rasm).
Tavlangan materialning sifati nafaqat uning mexanik xususiyatlari, balki qayta kristallangan donning o'lchami bilan ham belgilanadi. To'liq qayta kristallangan tuzilishdagi don hajmi bir xil. Qachon noto'g'ri belgilangan rejimlar Qayta kristallanish tavlanishi strukturada har xil o'lchamdagi ikkita dona guruhini aniq ko'rsatadi. Ushbu qo'shaloq tuzilma, ayniqsa, chuqur chizish, bükme yoki abraziv operatsiyalari va mahsulotning qirqish paytida istalmagan.
Don hajmi ma'lum bir chegaraga oshgani sayin, guruchning shtamplash qobiliyati yaxshilanadi, lekin sirt sifati yomonlashadi. Donadorligi 40 mikrondan ortiq bo'lgan mahsulot yuzasida xarakterli "apelsin qobig'i" pürüzlülüğü kuzatiladi.
Deformatsiyalangan strukturaning evolyutsiya bosqichlari vaqt o'tishi bilan sezilarli darajada uzaytiriladi va shuning uchun ko'rinadi qabul qilish mumkin tavlanish vaqtini o'zgartirib, mayda donali qisman yoki to'liq qayta kristallangan struktura. To'liq bo'lmagan qayta kristallangan tuzilishga ega va juda kichik don o'lchamiga ega bo'lgan yarim tayyor mahsulotlar "apelsin qobig'i" hosil bo'lmasdan muhrlanadi.
Qisman tavlanish, muddati dastlabki deformatsiya darajasi bilan belgilanadi, 250-400 ° S oralig'ida amalga oshiriladi. To'g'ri texnologik rejimni saqlab qolish uchun bunday tavlanishni ish harorati bo'lgan brosh pechlarida amalga oshirish kerak. va ushlab turish vaqti (broshlash tezligi) qat'iy nazorat qilinadi.
Qisman tavlanish, birinchi navbatda, "mavsumiy yorilish" deb ataladigan qoldiq stresslarni kamaytirish uchun ishlatiladi. 15% dan ortiq Zn ni o'z ichiga olgan guruchlarga xos bo'lgan korroziyaning bu turi bir vaqtning o'zida stress (qoldiq va qo'llaniladigan) va o'ziga xos kimyoviy reagentlar (masalan, ammiak eritmalari va bug'lari, eritmalar) ta'siri ostida kristallararo yoriqlarning bosqichma-bosqich rivojlanishidan iborat. simob tuzlari, nam sulfat angidrid, turli aminlar va boshqalar). Guruchlarning mavsumiy yorilishlarga sezgirligi ularning mutlaq kattaligiga emas, balki stressning bir xilligi bilan bog'liq deb ishoniladi.
Qoldiq kuchlanishlarni kamaytirish uchun tavlanishning samaradorligi simob sinovi bilan tekshiriladi. Simob sinov usuli qoldiq stresslar mavjudligini sifatli baholashni ta'minlaydi. Bunga asoslanadi turli xulq-atvor simob nitrat ta'sirida stressli va kuchlanishsiz material. Sinov paytida yalang'och ko'z bilan ko'rinadigan stressli materialda uzunlamasına va ko'ndalang yoriqlar paydo bo'ladi. Ular korroziya yorilishi natijasida mahsulotning ishlayotgan yoki saqlash vaqtida yo'q qilinishiga olib keladigan kuchlanish kuchlanishi joylarida paydo bo'ladi.
Qoldiq kuchlanishni kamaytirish uchun guruch uchun tavlanish rejimlari shaklda keltirilgan. 46 va jadvalda. 16.
Metallning qattiqlashishi uning tuzilishiga ba'zi o'zgarishlar kiritishga imkon beradi, uni yumshoqroq yoki aksincha, qattiqroq qiladi. Qattiqlashganda, ko'p narsa nafaqat isitishning o'ziga, balki sovutish jarayoniga va vaqtga ham bog'liq. Ishlab chiqaruvchilar asosan po'latni qattiqlashtiradi, bu esa mahsulotni yanada mustahkam qiladi, ammo agar kerak bo'lsa, mis ham qotib qolishi mumkin.
Misni qotirish - ishlab chiqarish jarayoni
Mis tavlanish usuli yordamida qattiqlashadi. Issiqlik bilan ishlov berish jarayonida mis kelajakda nima uchun ishlatilishiga qarab yumshoqroq yoki qattiqroq bo'lishi mumkin. Shu bilan birga, misni qattiqlashtirish usuli po'latni qotib qolish usulidan sezilarli darajada farq qilishini unutmaslik kerak.
Mis havoda sekin sovishi natijasida qattiqlashadi. Agar yumshoqroq strukturani olish zarur bo'lsa, u holda qattiqlashuv metallni isitishdan so'ng darhol suvda tez sovutish orqali amalga oshiriladi. Agar siz juda yumshoq metallni olishingiz kerak bo'lsa, unda siz misni qizarib ketguncha qizdirishingiz kerak (bu taxminan 600 °), keyin uni suvga tushiring. Mahsulot deformatsiya jarayonidan o'tib, kerakli shaklga ega bo'lgandan so'ng, uni yana 400 ° ga qizdirish va keyin havoda sovishini kutish mumkin.
Misni qattiqlashtiruvchi zavod
Misni qattiqlashtirish maxsus jihozlar shu maqsadda ishlab chiqilgan. Qattiqlashtiruvchi uskunalarning bir nechta turlari mavjud, ammo bugungi kunda indüksiyon uskunalari eng ommabop bo'ldi. Induksion o'rnatish misni qotish uchun juda yaxshi, bu sizga mahsulotni olish imkonini beradi yuqori sifatli. Avtomatlashtirilgan uchun rahmat dasturiy ta'minot HDTV uskunasi yuqori aniqlik bilan sozlangan, bu erda isitish vaqti, harorati, shuningdek, metallni sovutish usuli ko'rsatilgan.
Agar kompaniya doimo qattiqlashsa metall buyumlar, keyin qulay, tez qattiqlashuv uchun mo'ljallangan maxsus jihozlar to'plamiga e'tibor berish yaxshi bo'ladi. ELSIT qotish kompleksida hamma narsa bor zarur jihozlar HDTVni qattiqlashtirish uchun. Qattiqlashtiruvchi kompleks quyidagilarni o'z ichiga oladi: induksion o'rnatish, qattiqlashtiruvchi mashina, manipulyator va sovutish moduli. Agar mijoz turli shakldagi mahsulotlarni qattiqlashtirishi kerak bo'lsa, unda qattiqlashtiruvchi kompleksga turli o'lchamdagi induktorlar to'plami kiritilishi mumkin.
Rangli metallni issiqlik bilan ishlov berish deganda ma'lum bir haroratgacha qizdirish, so'ngra ma'lum tezlikda sovutish tushuniladi. Rangli metallga issiqlik bilan ishlov berishning umumiy samaradorligi uning oldingi ishloviga, harorat va isitish tezligiga, bu haroratda ta'sir qilish muddatiga va sovutish tezligiga bog'liq.
Rangli metallarga issiqlik bilan ishlov berish jarayonlarini ikkita asosiy guruhga bo'lish mumkin: issiqlik bilan ishlov berish, uning maqsadi muvozanat holatiga imkon qadar yaqin bo'lgan strukturani olish va issiqlik bilan ishlov berish, maqsadi: aksincha, muvozanatsizlik holatiga erishishdir. Ba'zi hollarda ikkala yuqorida aytib o'tilgan jarayonlar guruhi bir-birining ustiga chiqadi
Birinchi guruh o'z ichiga oladi qayta kristallanish tavlanishi deformatsiyalangan material, keyin ichki stressni bartaraf etish uchun tavlanish va nihoyat gomogenizatsiya tavlanishi kastinglar Ba'zan so'zning tor ma'nosida issiqlik bilan ishlov berish deb hisoblanadigan ikkinchi guruhga muvozanatsiz holatni olish bilan issiqlik bilan ishlov berish kiradi, ya'ni. dispersiyani davolash
Yumshoq yoki qayta kristallanish tavlanishi
Yumshoq tavlanish - sovuq ishlov berilgan ish qismlarini issiqlik bilan ishlov berish. Mahsulotni ma'lum bir haroratgacha qizdirish, ma'lum vaqt davomida bu haroratda ushlab turish va qoida tariqasida, asta-sekin, keyin sovutish orqali ishlab chiqariladi. Harorat darajasi, ushlab turish vaqti, shuningdek, isitish va sovutish tezligi ham oldingi ishlov berish usuliga, ham mahsulotning kerakli xususiyatlariga bog'liq. Binobarin, bu tavlanish jarayoni oldingi pasayish darajasi, tavlanishning harorati va davomiyligi va mahsulotning kerakli tuzilishi bilan tavsiflanadi. Buni quyidagi misollar bilan qisqacha tasvirlash mumkin:
Natijada qotib qolgan metall bosim bilan davolash, isitish vaqtida bir-biriga o'xshash bir nechta o'zgarishlarga uchraydi. Birinchidan, ichki stressni olib tashlash, ya'ni buzilishlarni bartaraf etish bilan tavsiflangan "tiklash" deb ataladigan narsa sodir bo'ladi. kristall panjara bosim bilan ishlov berish orqali materialda paydo bo'ladi. Bu mintaqada mexanik xususiyatlar juda kam o'zgaradi, garchi o'zgarishlar allaqachon ba'zi fizik xususiyatlarda kuzatilgan. Keyinchalik isitish bilan ular shakllana boshlaydi embrionlar yangi hosil qiluvchi tuzilish va bu embrionlarning o'sishi sodir bo'ladi. Birgalikda bu ikki jarayon deyiladi qayta kristallanish. Mexanik va jismoniy xususiyatlar, bosim bilan ishlov berish natijasida material tomonidan olingan, qayta kristallanish paytida yo'qoladi va material qattiqlashuvdan oldin bo'lgan xususiyatlarga ega bo'ladi. Shundan so'ng donning o'sish bosqichi keladi, unda kristallar birlashadi; bu holda ba'zi kristallar qo'shni kristallar hisobiga o'sadi va kristall strukturasi kattalashadi.
Kislorodsiz misning mexanik xossalarini sovuq qotish va qayta kristallanish bilan tavlanish jarayonida o'zgartirish jarayoni quyidagi grafiklarda tushuntirilgan.
Sovuq qotish paytida mexanik xususiyatlarning siqilish darajasiga bog'liqligi
Qayta kristallanish tavlanishida mexanik xususiyatlarning haroratga bog'liqligi
Oldingi pasayish darajasiga va haroratga qarab qattiqlik egri chiziqlari, shuningdek, qayta kristallanishdan keyin haroratga qarab don o'sishi
Ichki stressni bartaraf etish uchun tavlanish
Bu yumshatish deyiladi barqarorlashtirish, va deformatsiyalangan ish qismlariga nisbatan - dam olish. Tavlanish past haroratgacha qizdirishdan va mahsulot to'liq qizdirilgunga qadar bu haroratda qisqa vaqt ushlab turishdan, keyin esa sekin sovutishdan iborat. Bosim bilan ishlov beriladigan ish qismlari uchun bu tiklanish mintaqasidan, ya'ni qayta kristallanish haroratidan past haroratdir. Bu tavlanish, masalan, notekis sovutish va issiqlik bilan ishlov berish orqali quymalarda va sovuq bosim bilan ishlov berish, issiqlik bilan ishlov berish yoki katta chip qismlari bilan kesish orqali zarb qilingan buyumlarda yuzaga keladigan ichki kuchlanishlarni yo'q qiladi. Bu isitish vaqtida oldingi kristallanish saqlanib qoladi. Mexanik xususiyatlar ham uzoq muddatli saqlashdan keyin ham sezilarli darajada o'zgarmaydi.
Mahsulotlar, ayniqsa murakkab konfiguratsiyalar uchun bu jarayon o'lchovli barqarorlikni ta'minlaydi. Ba'zi ishlangan alyuminiy va mis qotishmalari uchun haroratni pasaytirishga misol 1-jadvalda keltirilgan
Ba'zi deformatsiyalanadigan metallar va qotishmalarda ichki kuchlanishlarni bartaraf etish uchun haroratni pasaytirish
Gomogenizatsiya tavlanishi
Gomogenlashtiruvchi tavlanish - bu yuqori haroratgacha qizdirishdan va bir xil tarkibga va bir xil tuzilishga erishilgunga qadar ma'lum vaqt davomida ushbu haroratda ushlab turishdan iborat issiqlik bilan ishlov berish. Bu odatda sekin sovutish bilan kuzatiladi. Quyma qotishmalarda topilgan notekislik (heterojenlik) ikki xil. Bu - aralashmalarni ajratish, quymaning oxirgi qotib qolgan qismlarida to'planib, va delaminatsiya (qatlamlash) qattiq eritmaning har bir alohida kristali. Kristal ichidagi nosimmetrikliklar osongina tekislanadi diffuziya, agar u etarlicha yuqori haroratda va etarlicha uzoq vaqt davomida sodir bo'lsa. Aksincha, quymaning alohida joylarida to'plangan aralashmalar kamroq yaxshi tavlanish orqali tarqaladi. Ular yuqori haroratda asosiy metallda erigan taqdirdagina diffuziyaga qodir. Ammo bu holatda ham, gomogenizatsiya jarayoni alohida zarralar bosib o'tishi kerak bo'lgan uzoq yo'l tufayli qiyin
Deformatsiyalangan metallar, shuningdek, agar ularning ba'zi mexanik xususiyatlarini yaxshilash zarur bo'lsa, gomogenizatsiya tavlanishiga duchor bo'lishi mumkin, ayniqsa yopishqoqlik Va kimyoviy qarshilik qotishma Yuqori haroratgacha qizdirish orqali ma'lum qotishma elementlari qotishma bir hil holga kelguncha qattiq eritmaga o'tkaziladi va keyin tez sovutish segregatsiyani bostiradi. Biroq, bu jarayon allaqachon nomutanosiblik holatini olish uchun issiqlik bilan ishlov berish sohasiga o'tmoqda
Dispersiyani davolash
Qotishmaning dispersion qattiqlashuvi uchun shart shundan iboratki, asosiy kristallar qisman eriydigan fazani o'z ichiga oladi, uning eruvchanligi haroratning pasayishi bilan kamayadi. Sekin sovutish bilan segregatsiya sodir bo'ladi, buning natijasida diagramma shakliga qarab, toza metall, birikmalarning qattiq eritmasi yoki boshqa faza. Qattiq eritma hududidan tez sovutish orqali ko'p hollarda segregatsiyani bostirish mumkin va shu tarzda o'chirilgan qotishma o'ta to'yingan qattiq eritmaning muvozanatsiz holatiga keltirilishi mumkin. Keyinchalik o'rtacha isitish yoki normal harorat bilan qotishma barqaror holatga erishadi. Ushbu murakkab jarayon hali to'liq tushunilmagan, garchi bir qator qotib qoladigan qotishmalar allaqachon amaliy texnologiyada qo'llanilgan. Davolanayotgan turli qotishmalar uchun jarayon har xil, ko'p hollarda, hatto bir xil qotishma uchun ham boshqacha davom etadi. Shuning uchun biz faqat o'zimizni cheklaymiz qisqacha tavsif bu jarayon
Quritish asosan uch bosqichdan iborat. Birinchidan, qotishma tegishli haroratgacha isitiladi. Bu harorat orasida solidus chizig'i va qattiq eruvchanlik chizig'i solidus haroratiga iloji boricha yaqinroq. Bu haroratni, ayniqsa alyuminiy qotishmalari uchun (490-535 ° C) tor diapazonini hisobga olgan holda, tuzli eritmada saqlash yaxshidir va shuning uchun aynan shu eritmalar ko'pincha qo'llaniladi. Ushbu turdagi tavlanishning maqsadi boy qattiq eritmani olishdir. Ushbu haroratda ushlab turish qotishma turiga va ish qismining turiga bog'liq. Shundan so'ng tez sovutish (yog'da yoki suvda söndürme) amalga oshiriladi. Qotishma muvozanat holatiga yaqinlashganda turli bosqichlardan o'tadi va o'ta to'yingan qattiq eritmaning atomlari har safar turlicha joylashadi. Bu jarayon normal yoki yuqori haroratlarda amalga oshiriladi; ba'zan qarish deb ataladi. Ba'zi hollarda sovuq ishlov berish qattiqlashuv va qarish o'rtasida amalga oshiriladi. Oddiy haroratlarda qarish deyiladi tabiiy, va yuqori haroratlarda - sun'iy
Qattiqlashuv jarayonida mexanik xususiyatlar o'zgaradi. Qattiqlashgandan so'ng, yopishqoqlik ortishi bilan mustahkamlik bir oz pasayadi va qarish bilan mustahkamlik yana ortadi va qattiqlik va egiluvchanlik biroz pasayadi. Qarish davridagi bu o'zgarishlar haroratga, qarish davomiyligiga va qotishma turiga qarab ma'lum naqshlarga bog'liq. Maksimalga erishgandan so'ng, qotishma kuchi yana qizdirilishi bilan yana pasayadi. Buning natijasida " haddan tashqari qarish» qotishma beqaror qotib qolgan holatdan muvozanat holatiga o'tadi va material o'zining oldingi mexanik xususiyatlarini oladi. Albatta, qotib qolgan holatdagi kuch har doim bir xil qotishmadan sovuq qotib qolish yo'li bilan olinishi mumkin bo'lganidan kattaroqdir va umuman olganda, qotib qoladigan qotishmalar ushbu guruhdagi boshqa metallarga nisbatan eng katta kuchga ega. Qattiqlashuv jarayonida ba'zi jismoniy xususiyatlar ham o'zgaradi.
5-rasmda harorat va sun'iy qarish davomiyligining ishlov berilgan AlMgSi qotishmasining mexanik xususiyatlariga ta'siri ko'rsatilgan.
Harorat va tavlanish davomiyligiga bog'liqligining umumiy diagrammasi turli yo'llar bilan ishlangan AlMgSi qotishmasini issiqlik bilan ishlov berish 6-rasmda ko'rsatilgan
Rangli metallarning ayrim qotishmalarida muvozanatsiz holatga qadar issiqlik bilan ishlov berilganda, xuddi po'latdagi kabi qayta kristallanish jarayonlari sodir bo'ladi. Misol uchun, ba'zi alyuminiy bronzalarda shunday deb ataladi fazali transformatsiyalar g - a, bu bilan bog'liq holda qattiqlashuv va temperaturadan iborat butun jarayonni chaqirish mumkin termal yaxshilanish. Yaxshilash paytida mexanik xususiyatlarning o'zgarishi qotib qolish bilan birga bo'lganlardan farq qiladi: so'ndirgandan so'ng mustahkamlik bir vaqtning o'zida pasayish bilan kuchayadi va chiniqtirish paytida mustahkamlik yana pasayadi, qattiqlik esa biroz ortadi.
Har xil issiqlik bilan ishlov berilgan deformatsiyalanadigan alyuminiy qotishmalarining mexanik xususiyatlarining qiymatlari
Qotishma darajasi | Yarim tayyor mahsulot | s t, (kg/mm2) | s vr, (kg/mm2) | d10, (%) |
---|---|---|---|---|
Al 99.5 | Varaq | 1,5 | 7 — 10 | 22 |
Al-Cu4-Mg1 | Varaq | 18 — 24 | 11 | |
Al-Zn6-Mg-Cu | Bar | 18 — 28 | 9 | |
Al-Mg-Si | Varaq | 11 — 15 | 16 | |
Al-Mg | Varaq | 18 — 23 | 16 | |
Al-Mg5 | Bar | 25 — 28 | 16 | |
Al-Mg-Mn | Varaq | 17 — 26 | 15 | |
Al-Mn | Quvur | 11 — 17 | 16 |
Qattiq holatda
Qotishma darajasi | Yarim tayyor mahsulot | s t, (kg/mm2) | s vr, (kg/mm2) | d10, (%) |
---|---|---|---|---|
Al 99.5 | Varaq | 11 | 13 | 4 |
Al-Mg-Si | Varaq | 15 | 17 | 4 |
Al-Mg | Varaq | 27 | 3 | |
Al-Mg5 | Bar | 28 | 32 | 3 |
Al-Mg-Mn | Varaq | 20 | 24 | 3 |
Al-Mn | Quvur | 19 | 3 |
Shifolangan holatda
Qotishma darajasi | Yarim tayyor mahsulot | s t, (kg/mm2) | s vr, (kg/mm2) | d10, (%) | Eslatmalar |
---|---|---|---|---|---|
Al-Cu4-Mg1 | Varaq | 28 | 43,5 | 10 | Oddiy haroratda quritiladi; barcha o'lchamlar |
Al-Cu-Ni-Mg-Fe | Soxtalashtirish | 26 | 38 | 4 | Kichik zarb va don yo'nalishi bo'yicha |
Al-Zn6-Mg-Cu | Bar | 38 | 50 | 6 | Yuqori haroratda davolanadi |
Al-Mg-Si | Varaq | 10 | 20 | 12 |
Issiqlik bilan ishlov berish rejimlari va quyma alyuminiy qotishmalarining mexanik xususiyatlarining qiymatlari
Qotishma darajasi | Kasting | Quymalarni issiqlik bilan ishlov berish usuli | Söndürme harorati (°C) | Ushbu haroratda ta'sir qilish muddati (soat) | Qarish harorati (°C) | Qarish davomiyligi (soat) | s t, (kg/mm2) | s vr, (kg/mm2) | d5, (%) | HB |
---|---|---|---|---|---|---|---|---|---|---|
Al-Si-Cu5 | Qumga | 180±5 | 15 | 16 | 65 | |||||
Al-Si-Cu5 | Qumga | Issiq quritilgan | 525±5 | 4 | 180±5 | 5 | 20 | 70 | ||
Al-Si-Cu5 | Qumga | 525 +5 -10 | 4 | 230±5 | 5 | 18 | 1 | 65 | ||
Al-Si-Cu5 | Sovuq qolipda | Sun'iy qarilik | 180±5 | 15 | 16 | 65 | ||||
Al-Cu-Si5 | Sovuq qolipda | Qattiqlashtirilgan va barqarorlashtirilgan | 525 +5 -10 | 4 | 230±5 | 5 | 18 | 1 | 65 | |
Al-Cu-Ni-Mg | Qumga | Issiq quritilgan | 515±5 | 4 — 10 | 235±5 | 4 — 6 | 18 | 22 | 0,3 | 90 |
Al-Cu-Ni-Mg | Sovuq qolipda | Issiq quritilgan | 515±5 | 4 — 10 | 235±5 | 4 — 6 | 20 | 24 | 0,3 | 90 |
Al-Mg11 | Qumga | Jahldor | 435±5 | 15 — 20 | 28 | 9 | 60 | |||
Al-Si13 | Qumga | Termal ishlov berilmagan | 8 | 17 | 4 | 50 | ||||
Al-Si13 | Sovuq qolipda | Tavlangan | 9 | 20 | 3 | 55 |
Eslatma: Mexanik xususiyat qiymatlari minimal qiymatlardir va maxsus quyma sinov tayoqlariga murojaat qiling
Deformatsiyalanadigan alyuminiy qotishmalari uchun issiqlik bilan ishlov berish rejimlari
Issiq deformatsiya
Qotishma darajasi | Optimal harorat (°C) | |
---|---|---|
Al 99.5 | 380 — 500 | 1 — 2 |
Al-Cu4-Mg1 | 400 — 450 | 4 — 8 |
Al-Cu-Ni-Mg-Fe | 420 — 470 | 4 — 8 |
Al-Zn6-Mg-Cu | 440 — 460 | 4 — 8 |
Al-Mg-Si | 480 — 520 | 2 — 4 |
Al-Mg | 400 — 450 | 2 — 4 |
Al-Mg5 | 330 — 400 | 3 — 6 |
Al-Mg-Mn | 400 — 450 | 2 — 4 |
Al-Mn | 450 — 500 | 1 — 2 |
To'liq quritish
Qotishma darajasi | Harorat (°C) | Ushbu haroratda ta'sir qilish muddati (soat) | Sovutish usuli |
---|---|---|---|
Al 99.5 | 360 — 400 | 2 — 6 | Havoda |
Al-Cu4-Mg1 | 330 — 420 | 1 — 6 | |
Al-Cu-Ni-Mg-Fe | 340 — 400 | 1 — 6 | Pechda sekin; tez sovutish 40 - 60 daraja / soat 200 ° S haroratgacha |
Al-Zn6-Mg-Cu | 420 — 440 | 2 | Pechda sekin; tez sovutish 30 - 50 ° / soat |
Al-Mg-Si | 360 — 400 | 4 — 8 | Pechda sekin; tez sovutish 60 - 100 daraja / soat 200 ° S haroratgacha |
Al-Mg | 360 — 400 | 2 — 4 | Havoda |
Al-Mg5 | 360 — 400 | 2 — 4 | Pechda sekin |
Al-Mg-Mn | 360 — 400 | 1/2 — 3 | Havoda |
Al-Mn | 500 - 550 (tez isitish) | 1 — 4 | Havoda |
Davolanish
Qotishma darajasi | Söndürme harorati (°C) | Ushbu haroratda ta'sir qilish muddati (soat) | Qarish harorati (°C) | Qarish davomiyligi (soat) |
---|---|---|---|---|
Al-Cu4-Mg1 | 490 — 505 | 1/4 - 1, hammom | Oddiy haroratda | 5 kun |
Al-Cu-Ni-Mg-Fe | 520 — 540 | 1/2 - 1, hammom | 180 — 195 | 12-14 soat |
Al-Zn6-Mg-Cu | 465 — 475 | 5 - 15 daqiqa, hammom; 10-30 daqiqa, havo pechi | 130 — 140 | 16 soat |
Al-Mg-Si | 520 — 535 | 1/3 - 1, hammom | 155 — 160 | 4-6 soat |
Turli xil issiqlik bilan ishlov berilgan mis qotishmalarining mexanik xususiyatlarining qiymatlari
Yumshoq holatda yoki issiq deformatsiyadan keyin
Qotishma darajasi | Yarim tayyor mahsulot | s t, (kg/mm2) | s vr, (kg/mm2) | d10, (%) |
---|---|---|---|---|
Cu 99,5 | Varaq | 20 | 30 | |
Cu-Sn 6 | Bar | 15 | 35 | 40 |
Ms (guruch) 90 | Varaq | 8 | 25 | 40 |
Ms (guruch) 70 | Varaq | 13 | 28 | 47 |
Ms (guruch) 63 | Shakllangan profil | 12 | 31 | 40 |
Cu-Ni2-Si | Bar | 10 | 25 | 30 |
Cu-Al 10-Fe-Ni | Bar | 40 | 65 | 5 |
Cu-Be (2,0%)-Co (0,3%) | Choyshab va novda | 17 — 25 | 42 — 52 | 35 — 50 |
Qattiq holatda
Qotishma darajasi | Yarim tayyor mahsulot | s t, (kg/mm2) | s vr, (kg/mm2) | d10, (%) |
---|---|---|---|---|
Cu 99,5 | Varaq | 16 | 30 | 4 |
Cu-Sn 6 | Bar | 45 | 50 | 8 |
Ms (guruch) 90 | Varaq | 20 | 35 | 8 |
Ms (guruch) 70 | Varaq | 30 | 45 | 15 |
Ms (guruch) 63 | Shakllangan profil | 35 | 42 | 15 |
Cu-Be (2,0%)-Co (0,3%) | Choyshab va novda | 52 — 60 | 63 — 70 | 10 — 20 |
Po'lat qismlarni tavlash
Po'lat qismini mexanik yoki plastik ishlov berishni osonlashtirish uchun uning qattiqligi tavlanish orqali kamayadi. To'liq tavlanish deb ataladigan narsa, qism yoki ishlov beriladigan qismning 900 ° C haroratgacha qizdirilishi, bu haroratda uni butun hajmi bo'ylab isitish uchun bir muncha vaqt ushlab turishi va keyin asta-sekin (odatda o'choq bilan birga) bo'lishidan iborat. ) xona haroratiga qadar sovutiladi.
Ishlov berish jarayonida qismda paydo bo'ladigan ichki kuchlanishlar past haroratli tavlanish yo'li bilan olib tashlanadi, bunda qism 500-600 ° S haroratgacha qizdiriladi va keyin pech bilan birga sovutiladi. Ichki stresslarni engillashtirish va po'latning qattiqligini biroz pasaytirish uchun to'liq bo'lmagan tavlanish qo'llaniladi - 750-760 ° C gacha qizdirish va keyinchalik sekin (shuningdek, o'choq bilan birga) sovutish.
Qattiqlashuv muvaffaqiyatsiz bo'lganda yoki boshqa metallni qayta ishlash uchun asbobni haddan tashqari qizdirish zarur bo'lganda (masalan, quyma temirni burg'ulash uchun mis matkapni haddan tashqari qizdirish kerak bo'lganda) tavlanish ham qo'llaniladi. Yuvish jarayonida qism qattiqlashish uchun zarur bo'lgan haroratdan bir oz pastroq haroratgacha isitiladi va keyin asta-sekin havoda sovutiladi. Natijada, qotib qolgan qism yana yumshoq bo'ladi va ishlov berishga mos keladi.
Mis ham issiqlik bilan ishlov beriladi. Bunday holda, misni yumshoqroq yoki qattiqroq qilish mumkin. Biroq, po'latdan farqli o'laroq, mis havoda sekin soviganida qotib qoladi va mis suvda tez soviganida yumshoq bo'ladi. Agar mis sim yoki trubka olovda qizg'ish (600 ° C) qizdirilsa va keyin tezda suvga botirilsa, mis juda yumshoq bo'ladi. Bergandan keyin kerakli shakl mahsulotni yana 400 ° C ga qadar olovda qizdirish va havoda sovishini kutish mumkin. Keyin sim yoki trubka mustahkam bo'ladi. Agar trubkani egish kerak bo'lsa, u tekislash va yorilishdan qochish uchun qum bilan mahkam to'ldiriladi.
Guruchni yumshatish uning egiluvchanligini oshiradi. Yuvilgandan so'ng, guruch yumshoq bo'ladi, osongina egiladi, uriladi va yaxshi cho'ziladi. Yuvish uchun u 600 ° C ga qadar isitiladi va xona haroratida havoda sovutiladi.
Duraluminning tavlanishi va qattiqlashishi
Duraluminni tavlash uning qattiqligini kamaytirish uchun amalga oshiriladi. Qism yoki ishlov beriladigan qism, qattiqlashuv paytida bo'lgani kabi, taxminan 360 ° C ga qadar isitiladi, biroz vaqt ushlab turiladi va keyin havoda sovutiladi. Tavlangan duraluminning qattiqligi qotib qolgan duraluminning deyarli yarmini tashkil qiladi.
Duraluminli qismning taxminan qizdirish harorati quyidagicha aniqlanishi mumkin: 350-360 ° S haroratda, qismning issiq yuzasi bo'ylab o'tkazilgan yog'och parchasi yonib ketadi va qorong'i iz qoldiradi. Qismning harorati uning yuzasiga qo'yilgan kichik (gugurt boshi o'lchamidagi) mis folga yordamida juda aniq aniqlanishi mumkin. 400 ° S haroratda folga ustida kichik yashil olov paydo bo'ladi.
Tavlangan duralumin past qattiqlikka ega; uni yoriqlardan qo'rqmasdan ikki marta shtamplash va egish mumkin.
Qattiqlashuv. Duralumin qotib qolishi mumkin. Qattiqlashganda, bu metalldan tayyorlangan qismlar 360-400 ° S ga qadar isitiladi, bir muddat ushlab turiladi, keyin xona haroratida suvga botiriladi va to'liq sovutilgunga qadar u erda qoldiriladi. Shundan so'ng darhol duralumin yumshoq va moslashuvchan bo'ladi, osongina egilib, soxtalashtiriladi. U uch-to'rt kundan keyin ortib borayotgan qattiqlikka ega bo'ladi. Uning qattiqligi (va ayni paytda mo'rtlik) shunchalik ko'payadiki, u kichik burchak ostida egilishga bardosh bera olmaydi.
Duralumin qarigandan keyin eng yuqori kuchga ega bo'ladi. Xona haroratida qarish tabiiy, yuqori haroratda esa sun'iy deb ataladi. Xona haroratida qoldirilgan yangi qotib qolgan duraluminning mustahkamligi va qattiqligi vaqt o'tishi bilan ortadi va besh-etti kundan keyin eng yuqori darajaga etadi. Bu jarayon duralumin qarishi deb ataladi.
<<<Назад
Alyuminiyni lehim yoki payvandlashmi? Farqi nima va qaysi biri yaxshiroq?
Birinchidan, ta'riflarni ko'rib chiqaylik. Payvandlash - bu atomlararo aloqalarni o'rnatish yo'li bilan yaxlit bo'g'inlarni ishlab chiqarish jarayoni. Lehimlash - qotishma, erituvchi lehim, masalan, birlashtirilgan metallarni eritib, qizdirilgan holatda metallarni birlashtirish jarayoni.
Boshqacha qilib aytganda, payvandlashda payvandlangan qismlarning qirralari eritiladi va keyin muzlatiladi. Lehimlashda oddiy metall faqat ma'lum bir haroratgacha qizdiriladi va qo'shma lehim va eritilgan metallarning sirt diffuziyasi va kimyoviy reaktsiyasi natijasida hosil bo'ladi.
Xo'sh, qaysi biri yaxshiroq, lehim yoki alyuminiy payvandlash?
Bu savolga javob berish uchun alyuminiy qotishmalarini lehimlash va payvandlashning asosiy usullarini, ularning afzalliklari va kamchiliklarini ko'rib chiqing.
Alyuminiyni payvandlash.
Alyuminiyni payvandlashda to'rt turdagi payvandlash eng ko'p qo'llaniladi:
1. Elektrod yoki TIG payvandlash. Iste'mol qilmaydigan elektrod sifatida volfram maxsus qotishma qo'shimchalar (lantan, serium va boshqalar) bilan ishlatiladi.
Ushbu elektrod orqali metallni eritadigan elektr yoyi paydo bo'ladi. Payvandlash paychalarining payvandlash hovuzi tomonidan qo'lda oziqlanadi. Butun jarayon an'anaviy gaz bilan payvandlash bilan juda o'xshash, faqat metall mash'alni yoqish bilan emas, balki himoya muhitda elektr yoyi bilan isitiladi. Bunday payvandlash faqat argon yoki geliy atmosferasida yoki ularning aralashmalarida amalga oshiriladi.
Argon va geliy payvandlash o'rtasida farq bormi? Ovqatlang. Xulosa shuki, geliy yanada ixcham yonish yoyi va shuning uchun asosiy metallarning chuqurroq va samaraliroq kirib borishini ta'minlaydi. Geliy qimmatroq va uning iste'moli argonga qaraganda ancha yuqori. Bundan tashqari, geliy juda suyuq, bu ishlab chiqarish, tashish va saqlash vaqtida qo'shimcha muammolarni keltirib chiqaradi.
Shuning uchun uni faqat payvand choklarining chuqur va samarali sintezi talab qilinadigan katta qismlarni payvandlashda himoya qiluvchi gaz sifatida ishlatish tavsiya etiladi. Amalda, geliy kamdan-kam hollarda inert gaz sifatida ishlatiladi, chunki argonda deyarli bir xil penetratsion effektga erishish mumkin, bu faqat payvandlash oqimini oshiradi. Alyuminiyning TIG payvandlashi odatda o'zgaruvchan tokni keltirib chiqaradi.
Nima uchun o'zgaruvchan tok bilan? Bu alyuminiy oksidi haqida, uning kichik miqdori muqarrar ravishda barcha turdagi payvandlashda mavjud. Gap shundaki, alyuminiyning erish nuqtasi taxminan 660 daraja. Alyuminiy oksidining erish nuqtasi 2060. Shuning uchun alyuminiy oksidi payvandlashda erishi mumkin emas - harorat etarli emas.
Va yuqori sifatli payvandlash oksidi uchun qo'llanma bo'lmaydi. Nima qilsa bo'ladi? Daromad tikuvni keraksiz aralashmalardan tozalash uchun juda qiziqarli xususiyatga ega bo'lgan geribildirim polaritesidan keladi. Bu xususiyat "katod dispersiyasi" deb ataladi. Shu bilan birga, teskari polaritli payvandlash oqimi juda past erish kuchiga ega. Shuning uchun, yoy, shuningdek, sezgir bo'lmagan, ammo erituvchi metallar bo'lishi uchun mo'ljallangan to'g'ri polaritning joriy komponentlarini ham o'z ichiga oladi.
Va oldinga va teskari qutbli oqimlarning almashinuvi o'zgaruvchan tok bo'lib, u ham tozalash, ham eritish xususiyatlarini birlashtiradi.
2. Sarflanadigan elektrodli payvandlash yoki yarim avtomatik payvandlash (MIG payvandlash). Bularning barchasi, qoida tariqasida, yagona doimiy "tozalash" yoy oqimlarining qutblarini almashtirish va volfram elektrodidan va to'g'ridan-to'g'ri payvandlash paytida eritilgan payvandlash paychalarining o'zidan o'tmaydigan yagona farq bilan payvandlashning ushbu turiga taalluqlidir. payvandlash.
Payvandlash uchun oddiy yarim avtomatik mashina qo'llaniladi, lekin simni oziqlantirish talablari yuqori. Ushbu turdagi payvandlash yuqori mahsuldorlik bilan ajralib turadi.
Qoplangan elektrodlar bilan qo'lda boshq payvandlash (MMA payvandlash). Qalinligi 4 mm va undan ortiq bo'lgan qattiq qismlarni payvandlash uchun ishlatiladi. U teskari polarit oqimiga qo'llaniladi va sifatsiz tikuvga ega.
4. Alyuminiyni gaz bilan payvandlash. U faqat cheklangan miqdordagi alyuminiy qotishmalarida qo'llanilishi mumkin, ular dahshatli payvandlash sifati bilan ajralib turadi. Bu juda qiyin va har bir odamning qo'lidan kelmaydi.
Amalda bu deyarli ishlatilmaydi.
Ekzotik payvandlashni yolg'iz qoldirib (ishqalanishli payvandlash, portlash payvandlash va plazma), payvandlangan birikmaning sifati va uning tarqalishi shakldan ancha oldinda, o'zgaruvchan tok argonli payvandlash.
Bu sof alyuminiy, duralumin, silan va boshqalarni bir necha millimetrdan bir necha santimetrgacha bo'lgan qotishmalarni payvandlash imkonini beradi. Bundan tashqari, u yadroviy payvandlash va boshqa alyuminiy qotishmalari uchun eng tejamkor va yagona hisoblanadi.
Alyuminiyni lehimlash
Odatda past haroratli (yumshoq qo'shma lehim) va yuqori haroratli (lehimli) lehim turini ajratadi.
Alyuminiy yumshoq lehimni lehimlash odatda oddiy lehimli temir bilan amalga oshiriladi va yuqori sinkli alyuminiy va oddiy qo'rg'oshin-qalay lehim uchun maxsus lehim sifatida ishlatilishi mumkin. Ushbu turdagi lehim bilan bog'liq asosiy muammo engil alyuminiy oksidiga qarshi kurashdir. Uni zararsizlantirish uchun har xil turdagi oqimlarni, lehim yog'larini va maxsus lehim turlarini qo'llash kerak. Ba'zi hollarda alyuminiyning yuzasi allaqachon an'anaviy lehim bilan lehimlangan nozik bir mis qatlami bilan qoplangan.
Biroq, galvanik qoplamalardan foydalanish texnologik jihatdan mumkin emas va iqtisodiy jihatdan mumkin emas. Qanday bo'lmasin, alyuminiy qotishmalarini past haroratlarda lehimlash juda qiyin va lehim birikmalarining sifati odatda o'rtacha darajadan yuqori. Bundan tashqari, metallarning heterojenligi tufayli, bog'langan birikma korroziyaga moyil bo'lib, har doim lak yoki bo'yoq bilan qoplangan bo'lishi kerak. Yuklangan tizimlarda yumshoq birikma lehimidan foydalanish mumkin emas.
Xususan, u konditsioner radiatorlarini ta'mirlash uchun ishlatilmasligi kerak, lekin radiator motorlarini ta'mirlash uchun ishlatilishi mumkin.
Alyuminiyni yuqori haroratda lehimlash. Zavodlarda alyuminiy radiatorlarni lehimlashda lehim ishlatiladi. Uning xarakteristikasi shundaki, lehimning erish nuqtasi metallning erish nuqtasidan atigi 20-40 daraja past bo'ladi. Ushbu lehim odatda lehimlash uchun ishlatiladigan maxsus yuqori harorat pastasini (masalan, neylon) o'z ichiga oladi va keyin himoya gaz muhitida maxsus pechlarda sinterlanadi.
Ushbu lehimlash jarayoni yuqori quvvat va hosil bo'lgan bo'g'inlarning past korroziyaga chidamliligi bilan tavsiflanadi, chunki lehim asosiy metallga yaqin kompozitsion sifatida ishlatiladi. Ushbu turdagi lehim yupqa devorli mahsulotlar uchun juda mos keladi, ammo uning texnologiyasi ancha murakkab va ta'mirlash uchun mutlaqo foydasizdir.
Yuqori haroratli alyuminiy lehimlashning ikkinchi turi gaz olovi bilan payvandlashdir. Lehim sifatida maxsus o'z-o'zidan tejamkor novdalar ishlatiladi (masalan, HTS 2000, Castolin 21 F va boshqalar).
Isitish uchun asetilen, propan va tercihen vodorod olovi (gidroliz) ishlatiladi. Bu erda texnologiya quyidagicha. Birinchidan, mash'al olovi metallni isitadi, so'ngra lehimli temir ehtiyotkorlik bilan lehim maydoniga to'ldiriladi. Rod eriganida, olov chiqariladi. Rodning erish nuqtasi taglik plitasining haroratidan ancha past emas, shuning uchun uni olib tashlashning oldini olish uchun uni yaxshilab isitish kerak.
Shuni ta'kidlash kerakki, bu turdagi lehim juda va juda qimmat va 300 dollargacha bo'lishi mumkin. 1 kilogramm uchun. Odatda u mahalliy ta'mirlash uchun ishlatiladi.
Xo'sh, qaysi biri yaxshiroq?
Nonvoy uyda eriydi: bosqichma-bosqich, video
Alyuminiyni lehimlash yoki payvandlashmi? Endi biz bu savolga javob bera olamiz. Metalllarning qalinligi 0,2-0,3 mm dan ortiq bo'lsa, u holda argonli payvandlashdan foydalaning. Xususan, oddiy ko'plab chuqurchalar balzam emitentlari, tovoqlar, qanotlar, qavslar, qotishma g'ildiraklar, Rulda, dvigatel boshi va boshqalarni argon bilan payvandlash natijasida payvand. Bu monolit, kimyoviy jihatdan chidamli va kuchli bog'lanishdir.
Metalllarning qalinligi 0,2-0,3 mm dan kam bo'lsa, alyuminiyning yuqori haroratli lehimidan foydalanish yaxshidir. Birinchidan, u argon bilan ichish juda qiyin bo'lgan dvigateldan yupqa chuqurchalar devor radiatorlarini lehimlash uchun ishlatiladi. Past haroratli yumshoq lehim, agar umuman ishlatilmasa, yaxshiroqdir, chunki bu bo'g'inlar ancha zaif va kimyoviy jihatdan kamroq chidamli.
Bundan tashqari, past haroratli lehimlashda ishlatiladigan kislota oqimlari ham oddiy metallarni, ham lehim birikmalarini nisbatan qisqa vaqt ichida yo'q qilishi mumkin.
Ko'pgina metallarni issiqlik bilan ishlov berish orqali mustahkamlash mumkin emas. Biroq, deyarli barcha metallar - ma'lum darajada - zarb, prokat yoki bükme orqali mustahkamlanadi. Bunga metallning sovuq qotishi yoki qattiqlashishi deyiladi.
Tavlash - qotib qolgan metallni yumshatish uchun issiqlik bilan ishlov berishning bir turi bo'lib, u sovuq ishlov berishda davom etishi mumkin.
Sovuq ishlov berish: mis, qo'rg'oshin va alyuminiy
Oddiy metallar deformatsiyaning qattiqlashuv darajasi va tezligi bo'yicha juda katta farq qiladi - sovuq yoki sovuq qattiqlashuv.
Mis sovuq zarb qilish natijasida juda tez qotib qoladi va shuning uchun uning egiluvchanligi va egiluvchanligini tezda pasaytiradi. Shuning uchun mis tez-tez tavlanishni talab qiladi, shuning uchun uni yo'q qilish xavfisiz qayta ishlash mumkin.
Boshqa tomondan, qo'rg'oshinni tavlanmasdan yoki uni buzish xavfisiz deyarli har qanday shaklga bolg'a bilan urish mumkin.
Qo'rg'oshin shunday egiluvchanlik zahirasiga ega bo'lib, u juda past darajada deformatsiyaning qattiqlashishi bilan katta plastik deformatsiyalarni olish imkonini beradi. Biroq, mis qo'rg'oshinga qaraganda qattiqroq bo'lsa-da, u odatda ko'proq egiluvchan.
Alyuminiy egiluvchanlik xususiyatlarini tiklash uchun tavlanishidan oldin bolg'acha shakllantirish yoki sovuq haddeleme orqali juda katta miqdordagi plastik deformatsiyaga bardosh bera oladi.
Sof alyuminiy misga qaraganda sekinroq qattiqlashadi va ba'zi alyuminiy qotishmalari juda qattiq yoki mo'rt bo'lib, qattiq qotib qolishga imkon beradi.
Temir va po'latni sovuq ishlov berish
Sanoat sof temirni keyinchalik qayta ishlash uchun juda qiyin bo'lgunga qadar katta deformatsiyaga qadar sovuq ishlov berish mumkin.
Temir yoki po'latdagi aralashmalar metallning sovuq ishlov berish qobiliyatini shu darajada buzadiki, ko'pchilik po'latlarni sovuq ishlov berish mumkin emas, albatta, avtomobil sanoati uchun maxsus past karbonli po'latlardan tashqari. Shu bilan birga, deyarli barcha po'latni qizil-issiq holatda plastik tarzda muvaffaqiyatli qayta ishlash mumkin.
Nima uchun metallni yumshatish kerak?
Metall duchor bo'lgan tavlanish jarayonining aniq tabiati ko'p jihatdan tavlangan metallning maqsadiga bog'liq.
Ko'p miqdorda po'lat po'lat ishlab chiqariladigan zavodlarda tavlanish va faqat bir qismi bunday ishlov berishni talab qiladigan kichik avtota'mirlash ustaxonasida tavlanish o'rtasida sezilarli farq bor.
Qisqacha aytganda, sovuq ishlov berish - bu metallning don tuzilishini yo'q qilish yoki buzish orqali plastik deformatsiya.
Yuvish jarayonida metall yoki qotishma qayta kristallanish sodir bo'ladigan haroratga qizdiriladi - yangi donlarning shakllanishi - eski - deformatsiyalangan va cho'zilgan - donalar o'rniga deformatsiyalanmagan va yumaloq. Keyin metall berilgan tezlikda sovutiladi. Boshqacha qilib aytadigan bo'lsak, sovuq plastmassa bilan ishlov berish paytida joyidan yoki deformatsiyaga uchragan metall ichidagi kristallar yoki donalar qayta tartibga solish va tabiiy holatiga qaytish imkoniyatiga ega, ammo yuqori tavlanish haroratida.
Temir va po'latni tavlash
Temir va yumshoq po'latlarni 900 daraja Selsiy bo'yicha haroratgacha qizdirish kerak va keyin iloji boricha "yumshoq" bo'lishini ta'minlash uchun sekin sovishini ta'minlash kerak.
Shu bilan birga, metallning sirtini oksidlanishiga yo'l qo'ymaslik uchun havo bilan aloqa qilishning oldini olish choralari ko'riladi. Bu kichik avtoulovlarni ta'mirlash ustaxonasida amalga oshirilganda, buning uchun iliq qum ishlatiladi.
Yuqori uglerodli po'latlar shunga o'xshash ishlov berishni talab qiladi, faqat ular uchun tavlanish harorati pastroq va taxminan 800 daraja Selsiy.
Misning tavlanishi
Mis quyuq qizil rangga qizdirilganda, taxminan 550 daraja Selsiyda tavlanadi.
Qizdirilgandan so'ng, mis suvda sovutiladi yoki havoda sekin sovishini ta'minlaydi. Yuvish haroratida qizdirilgandan keyin misning sovutish tezligi olingan ushbu metallning "yumshoqlik" darajasiga ta'sir qilmaydi. Tez sovutishning afzalligi shundaki, u metallni shkala va kirdan tozalaydi.
Alyuminiyni yumshatish
Alyuminiy 350 daraja Selsiy haroratda tavlanadi.
Rangli qotishmalarni issiqlik bilan ishlov berish
Zavodlarda bu mos pechlarda yoki tuzli vannalarda amalga oshiriladi. Ustaxonada alyuminiy gaz mash'alasi bilan tavlanadi. Ularning aytishicha, bu qizdirilgan metall yuzasiga yog'och parchasini ishqalashni o'z ichiga oladi.
Yog'och qora izlar qoldirishni boshlaganda, bu alyuminiy o'zining tavlanishini olganligini anglatadi. Ba'zan yog'och o'rniga sovun ishlatiladi: sovun jigarrang izlarni qoldirishni boshlaganda, isitishni to'xtatish kerak. Keyin alyuminiy suvda sovutiladi yoki havoda sovutish uchun qoldiriladi.
Ruxning tavlanishi
Rux 100 dan 150 darajagacha bo'lgan haroratlarda yana egiluvchan bo'ladi.
Bu shuni anglatadiki, uni qaynoq suvda pishirish mumkin. Sink issiq bo'lganda qayta ishlanishi kerak: u soviganida u o'zining moslashuvchanligini yo'qotadi.
Mis turli maqsadlar uchun mahsulotlar ishlab chiqarishda keng qo'llaniladi: idishlar, quvurlar, elektr taqsimlash qurilmalari, kimyoviy uskunalar va boshqalar. Misning turli xil qo'llanilishi uning maxsus jismoniy xususiyatlari bilan bog'liq.
Mis yuqori elektr va issiqlik o'tkazuvchanligiga ega va korroziyaga chidamli. Misning zichligi 8,93 N/sm3, erish temperaturasi 1083°, qaynash temperaturasi 2360°C.
Misni payvandlashdagi qiyinchiliklar uning fizik va kimyoviy xossalari bilan bog'liq4. Mis o'tga chidamli oksidlar hosil bo'lishi, gazlarni erigan metall tomonidan singdirilishi bilan oksidlanishga moyil, yuqori issiqlik o'tkazuvchanligiga va qizdirilganda sezilarli chiziqli kengayish koeffitsientiga ega.
Oksidlanish tendentsiyasi payvandlash vaqtida eritilgan metallni oksidlanishdan himoya qiluvchi va hosil bo'lgan oksidlarni eritib, ularni cürufga aylantiradigan maxsus oqimlardan foydalanishni talab qiladi.
Yuqori issiqlik o'tkazuvchanligi po'latni payvandlashdan ko'ra kuchliroq olovdan foydalanishni talab qiladi. Cu ning payvandlanishi uning tozaligiga bog'liq bo'lib, Cu ning payvandlanishi ayniqsa uning tarkibida B1, Pb, 3 va Oz borligi bilan buziladi. rg ning tarkibi Cu sinfiga qarab 0,02 dan 0,15% gacha, III va Pb mis mo'rtligini va qizil mo'rtligini beradi Cu20 mis oksidi shaklida kislorodning mavjudligi metallning mo'rt qatlamlarini hosil qiladi. va termal zonada paydo bo'ladigan yoriqlar ta'sir qiladi.
Mis oksidi past erish nuqtasiga ega bo'lgan mis bilan past eriydigan evtektika hosil qiladi. Evtektika mis donalari atrofida joylashadi va shu bilan donalar orasidagi bog'lanishni zaiflashtiradi.
Misni payvandlash jarayoniga nafaqat misda erigan kislorod, balki atmosferadan so'rilgan kislorod ham ta'sir qiladi. Bunda mis oksidi CuO bilan birga mis oksidi CuO hosil bo'ladi. Payvandlashda bu oksidlarning ikkalasi ham gaz bilan payvandlashni qiyinlashtiradi va oqim yordamida olib tashlanishi kerak.
Vodorod va uglerod oksidi Cu payvandlash jarayoniga ham salbiy ta'sir qiladi.
Ularning mis oksidi CuO bilan o'zaro ta'siri natijasida suv bug'lari va karbonat angidrid hosil bo'lib, ular payvandlash metallida teshiklarni hosil qiladi. Ushbu hodisani oldini olish uchun misni payvandlash qat'iy oddiy olov bilan amalga oshirilishi kerak. Si qanchalik toza va 0-2 dan kam bo'lsa, u yaxshi payvandlanadi.
GOST 859-78 bo'yicha sanoatda payvandlangan konstruksiyalarni ishlab chiqarish uchun Oa- (0,01% gacha) miqdori kamaytirilgan M1r, M2r MZr mis markalari ishlab chiqariladi.
C gazli payvandlashda dumba va burchakli birikmalar qo'llaniladi va T-bo'g'inlar yaxshi natija bermaydi;
Payvandlashdan oldin payvandlangan qirralarni payvandlash joyidan kamida 30 mm masofada axloqsizlik, yog ', oksidlar va boshqa ifloslantiruvchi moddalardan tozalash kerak. Payvandlash joylari qo'lda yoki mexanik ravishda po'lat cho'tkalar bilan tozalanadi. Qalinligi 8 mm gacha bo'lgan misni payvandlash qirralarning kesilmasdan amalga oshiriladi va qalinligi 3 mm dan ortiq bo'lsa, qo'shilishning har bir tomonida 45 ° burchak ostida X shaklidagi qirralarning kesilishi talab qilinadi. To'mtoqlik uni payvandlanayotgan metall qalinligining 0,2 ga teng qiladi. Eritilgan holatda misning suyuqligi oshganligi sababli, yupqa choyshablar bo'shliqsiz payvandlanadi va 6 mm dan ortiq choyshablar grafit va uglerod tagliklarida payvandlanadi.
Qalinligi 4 mm gacha bo'lgan misni payvandlashda payvandlash olovining kuchi 8-10 mm gacha bo'lgan qalinligi uchun payvandlanadigan metallning 1 mm qalinligi uchun 150-175 dm3 / soat asetilen iste'moli asosida tanlanadi; quvvat 175-225 dm8 / soatgacha oshiriladi.
Katta qalinliklar uchun ikkita mash'al bilan payvandlash tavsiya etiladi - biri isitish uchun, ikkinchisi esa payvandlash uchun. Issiqlik tarqalishini kamaytirish uchun payvandlash asbest tagida amalga oshiriladi. Issiqlikdan ta'sirlangan zonaga olib tashlash natijasida katta issiqlik yo'qotishlarini qoplash uchun payvandlangan qirralarning dastlabki va bir vaqtning o'zida isitilishi qo'llaniladi.
Qirralar bir yoki bir nechta burner bilan isitiladi.
C ni payvandlash uchun alanga mutlaqo normal tanlanadi, chunki oksidlovchi olov kuchli oksidlanishni keltirib chiqaradi va karbüruvchi olov bilan teshiklar va yoriqlar paydo bo'ladi. Olov yumshoq bo'lishi kerak va po'latni payvandlashdan ko'ra kattaroq burchakka yo'naltirilishi kerak. Payvandlash qayta tiklash zonasida amalga oshiriladi, yadro uchidan payvandlanadigan metallgacha bo'lgan masofa 3-6 mm.
Payvandlash jarayonida qizdirilgan metall har doim olov bilan himoyalangan bo'lishi kerak. Payvandlash chap va o'ng usullar yordamida amalga oshiriladi, ammo misni payvandlashda to'g'ri usul eng maqbuldir. Payvandlash maksimal tezlikda uzilishlarsiz amalga oshiriladi.
Payvandlash yuqoriga qarab amalga oshiriladi. Mash'al og'iz bo'shlig'ining payvandlanayotgan mahsulotga moyillik burchagi 40-50 °, to'ldiruvchi sim esa 30-40 °. Vertikal tikuvlarni tayyorlashda mash'alning og'iz qismining egilish burchagi 30 ° ni tashkil qiladi va payvandlash pastdan yuqoriga qarab amalga oshiriladi. Misni payvandlashda qismlarni tirgaklar bilan mahkamlash tavsiya etilmaydi. Uzoq tikuvlar teskari bosqichli usul yordamida erkin holatda payvandlanadi.
Misni gaz bilan payvandlash faqat bitta o'tishda amalga oshiriladi.
To'ldiruvchi simning tarkibi gazni payvandlash jarayoniga katta ta'sir ko'rsatadi. Payvandlash uchun qo'shimcha sifatida GOST 16130-72 ga muvofiq novdalar va simlar qo'llaniladi: M1, MSr1, MNZh5-1, MNZHKT5-1-0,2-0,2.
Xato 503 Xizmat mavjud emas
Payvandlash simi MSr1 tarkibida 0,8-1,2% kumush mavjud. To'ldiruvchi simning diametri payvandlanadigan metallning qalinligiga qarab tanlanadi va 0,5-0,75 8 ga teng olinadi, bu erda 5 - metallning qalinligi, mm, lekin 8 mm dan oshmasligi kerak.
Payvandlash simi silliq, chayqalishsiz erishi kerak. To'ldiruvchi simning erish harorati asosiy metallning erish haroratidan past bo'lishi maqsadga muvofiqdir. Cu ni oksidlanishdan himoya qilish, shuningdek, deoksidlanish va hosil bo'lgan oksidlarni cürufga olib tashlash uchun payvandlash oqim bilan amalga oshiriladi. Fluxlar bor va natriy oksidlari va tuzlaridan tayyorlanadi. Cu payvandlash uchun fluxlar kukun, pasta va gazsimon shaklda qo'llaniladi, fosfor kislotasi tuzlarini o'z ichiga olgan 5 va 6-sonli oqimlarni fosfor va kremniy deoksidlovchi moddalari bo'lmagan sim bilan payvandlashda ishlatish kerak.
Si payvandlash BM-1 gazli oqimi yordamida ham amalga oshirilishi mumkin, bu holda isitish tezligini kamaytirish va payvandlash olovining kuchini oshirish uchun mash'al uchini bir raqamga oshirish kerak; Gazli oqimdan foydalanganda KGF-2-66 o'rnatilishi qo'llaniladi. Chang oqimi payvandlash joyiga payvand o'qining har ikki tomoniga 40-50 mm sepiladi. Xamir shaklidagi oqim payvandlanadigan metallning chetlariga va plomba novdasiga qo'llaniladi. Oqim qoldiqlari tikuvni 2% nitrat yoki sulfat kislota eritmasi bilan yuvish orqali chiqariladi.
Depozit qilingan metallning mexanik xususiyatlarini yaxshilash va zichligini oshirish va.
Payvand chokining plastisitivligini ta'minlash uchun payvandlashdan keyin payvandlash metallini zarb qilish tavsiya etiladi. Qalinligi 4 mm gacha bo'lgan qismlar sovuq holatda va kattaroq qalinlikda - 550-600 ° S haroratgacha qizdirilganda zarb qilinadi.
Zarbdan keyin tikuvni qo'shimcha yaxshilash issiqlik bilan ishlov berish - 550-600 ° S ga qadar isitish va suvda sovutish orqali ta'minlanadi. Payvandlanadigan mahsulotlar payvandlash mash'alasi yoki pechda isitiladi. Yuvishdan so'ng, payvandlangan metall qattiq bo'ladi.
⇐ Oldingi27282930313233343536Keyingi ⇒
Nashr qilingan sana: 2015-01-26; O'qilgan: 455 | Sahifaning mualliflik huquqining buzilishi
studopedia.org - Studopedia.Org - 2014-2018 (0,001 s)…
Bosh sahifa>>Rangli metallarni payvandlash>>Mis va po'latni payvandlash
Mis va uning qotishmalarini po'lat bilan payvandlash. Mis va po'latni qanday payvand qilish kerak?
Amalda, mis va po'latni payvandlash ko'pincha dumba bo'g'inlarida amalga oshiriladi. Tuzilishning tabiatiga qarab, bunday ulanishdagi tikuvlar tashqi yoki ichki bo'lishi mumkin.
Guruchni po'latga payvandlash uchun gaz bilan payvandlash eng mos keladi va qizil misni po'latga payvandlash uchun metall elektrodlar bilan elektr boshq payvandlash.
Oqim qatlami ostida uglerod elektrodlari bilan payvandlashda va BM-1 suv osti yoyi ostida gaz bilan payvandlashda ham yaxshi natijalarga erishiladi. Ko'pincha amalda guruchni po'latga gaz bilan payvandlash plomba moddasi sifatida mis yordamida amalga oshiriladi.
Rangli metall va po'latdan bir xil qalinlikdagi payvandlangan qirralarning tayyorlash qora metallarni payvandlash bilan bir xil tarzda amalga oshiriladi.
Qalinligi 3 mm dan kam bo'lgan choyshablarni payvandlash kesishsiz amalga oshiriladi va 3 mm dan boshlanadigan choyshablar qirrali qirralar bilan payvandlanadi.
Agar qirralar etarli darajada kesilmagan bo'lsa yoki payvandlanadigan qismlarning uchlarida ifloslanish bo'lsa, yaxshi penetratsiyaga erishib bo'lmaydi. Shunga asoslanib, X shaklidagi truba qilingan katta qalinlikdagi qismlarni payvandlashda to'mtoq qilmaslik kerak.
Misni po'lat bilan payvandlash murakkab vazifadir, ammo sirtni qoplash va payvandlash uchun juda mumkin, masalan, kimyoviy uskunalar qismlari, po'lat blokli mis sim.
Bunday bo'g'inlarni payvandlash sifati ularga qo'yiladigan talablarga javob beradi. Misning mustahkamligini uning tarkibiga 2% gacha temirni kiritish orqali oshirish mumkin. Ko'proq temir bilan kuch pasayishni boshlaydi.
Uglerod elektrodi bilan payvandlashda to'g'ridan-to'g'ri polaritning to'g'ridan-to'g'ri oqimidan foydalanish kerak.
Elektr yoyining kuchlanishi 40-55V, uzunligi esa taxminan 14-20 mm. Payvandlash oqimi elektrodning diametri va sifatiga (uglerod yoki grafit) mos ravishda tanlanadi va 300-550A oralig'ida bo'ladi. Amaldagi oqim misni payvandlash bilan bir xil, bu oqimlarning tarkibi ushbu sahifada keltirilgan;
Oqim payvandlash zonasiga kiritilib, uni truba ichiga quyiladi.
Payvandlash usuli "chapda" ishlatiladi.
Mis shinalari po'latga payvandlashda eng yaxshi natijalar "qayiqda" payvandlashda olinadi. Bunday payvandlashning diagrammasi rasmda ko'rsatilgan. Birinchidan, mis qirralari uglerod elektrodi bilan isitiladi, so'ngra elektrod va plomba tayog'ining ma'lum bir pozitsiyasi bilan payvandlanadi (rasmga qarang). Payvandlash tezligi soatiga 0,25 m. Misni quyma temir bilan payvandlash bir xil texnologik usullardan foydalangan holda amalga oshiriladi.
Kichik qalinlikdagi (1,5 mm gacha) past qotishma bronzani qalinligi 2,5 mm gacha bo'lgan po'latga payvandlash argon muhitida iste'mol qilinmaydigan volfram elektrod bilan bir-birining ustiga yopishtiruvchi to'ldiruvchi simli avtomatik mashinada amalga oshirilishi mumkin. yon tomondan ta'minlangan 1,8 mm diametrli.
Bunday holda, yoyni mis tomondan bir-birining ustiga chiqishga yo'naltirish juda muhimdir. Bunday payvandlash usullari: oqim 190A, kamon kuchlanishi 11,5V, payvandlash tezligi 28,5m/soat, simni uzatish tezligi 70m/soat.
Mis va guruchni po'latga yaxshi payvandlangan payvandlash yordamida payvandlash mumkin.
Ushbu payvandlash usuli bilan po'lat qirralar juda kuchli eriydi va rangli metall qirralari biroz eriydi. Ushbu holatni hisobga olgan holda va ushbu metallarning qarshiligidagi farqni hisobga olgan holda, po'lat uchun 3,5 d, guruch uchun 1,5 d, mis uchun 1,0 d, bu erda d - payvandlanadigan novdalarning diametrlari olinadi. .
Qarshilik usuli yordamida bunday novdalarni payvandlash uchun po'lat uchun 2,5d, guruch uchun 1,0d va mis uchun 1,5d oshib ketish tavsiya etiladi. Turar joyning o'ziga xos qarshiligi 1,0-1,5 kg / mm2 oralig'ida qabul qilinadi.
Amalda, ko'pincha mis va uning qotishmalaridan yasalgan diametri 8-12 mm bo'lgan tirgaklarni po'latga yoki po'lat tirgaklarni mis mahsulotlarga payvandlash kerak bo'ladi.
Bunday payvandlash oldindan qizdirilmasdan OSTS-45 markasining nozik oqimi ostida teskari polaritning to'g'ridan-to'g'ri oqimi yordamida amalga oshiriladi.
Diametri 12 mm gacha bo'lgan mis tirgaklar yoki L62 markali guruch tirgaklar, diametri 10 mm gacha, oqim kuchi 400 A bo'lgan po'lat yoki quyma temirga yaxshi payvandlanadi.
Va LS 59-1 rusumli guruchdan tayyorlangan tirgaklar payvandlash uchun ishlatilmaydi.
Chelik tirgaklar mis va guruch mahsulotlariga yomon payvandlanadi.
Uyda misni qanday payvandlash mumkin?
Agar siz diametri 8 mm gacha bo'lgan pinning uchiga 4 mm balandlikdagi mis halqa qo'ysangiz, u holda metallarni payvandlash jarayoni qoniqarli davom etadi. Broze markasi Br uchun diametri 12 mm bo'lgan bir xil tirgaklar. OF 10-1 yaxshi payvandlanadi. Mis va po'latni boshq payvandlash uchun eng yaxshi natijalar K-100 elektrodlari tomonidan ta'minlanadi.
Guruchni yumshatish, qattiqlashtirish va issiqlik bilan ishlov berish bilan qiziqasizmi? Yetkazib beruvchi Evek GmbH keng assortimentda guruchni arzon narxda sotib olishni taklif qiladi. Biz mahsulotlarni qit'aning istalgan nuqtasiga yetkazib berishni ta'minlaymiz. Narx optimal.
Texnologiyani tanlash
Guruchni issiqlik bilan ishlov berish turlari qotishma tarkibidagi ruxning ulushi, shuningdek, fazaviy diagramma turi, qotishma qaysi turdagi guruchga tegishli - bir fazali yoki ikki fazali bilan belgilanadi. Yetkazib beruvchi Evek GmbH mahalliy va xorijiy ishlab chiqarilgan guruch prokat mahsulotlarini keng assortimentda arzon narxlarda sotib olishni taklif qiladi. Biz mahsulotlarni qit'aning istalgan nuqtasiga yetkazib berishni ta'minlaymiz. Narx optimal.
Bir fazali (oddiy) guruchlarni issiqlik bilan ishlov berish
Bunday navlar uchun qayta kristallanish yoki an'anaviy tavlanish qo'llaniladi. Maqsad - materialning plastik deformatsiyasi paytida paydo bo'lishi mumkin bo'lgan ichki stresslarni bartaraf etish. Yuvish rejimi qotishmadagi sink kontsentratsiyasiga bog'liq: bu parametrning oshishi bilan kerakli issiqlik bilan ishlov berish harorati pasayadi, lekin 300 ° C dan oshmaydi. Yuvishning samaradorligi mikrostrukturadagi yakuniy don hajmiga bog'liq. Ular metall-instrumental mikroskopning ko'rsatkichlari bo'yicha yoki GOST 5362 da berilgan mos yozuvlar tuzilmalariga muvofiq o'rnatiladi.
Yuvish muhiti
Kislorodning sezilarli miqdorini o'z ichiga olgan oddiy atmosferada issiqlik bilan ishlov berish tavsiya etilmaydi. Bu don hajmining notekis kamayishiga olib keladi va qotishma yuzasida oksidli dog'lar aniq ko'rinadi, ular qotishmani ortofosfor kislotasi yoki kaliy dixromat eritmasida o'chirish orqali olib tashlanishi kerak. Yana samarali issiqlik bilan ishlov berish usuli vakuumli tavlanish yoki inert gazlarning himoya atmosferasidan foydalanish hisoblanadi. Shu bilan birga, sinkning yonishi kamayadi.
Ikki fazali guruchlarni issiqlik bilan ishlov berish
Ko'p fazali guruchlar ruxdan boshqa qotishma elementlarni qo'shish orqali olinadi - temir, alyuminiy, qo'rg'oshin va boshqalar. Har bir guruch navining o'ziga xos qayta kristallanish tavlanish harorati mavjud. Eng ko'p ishlatiladigan rejimlar:
Sotib olish. Yetkazib beruvchi, narx
Guruchni yumshatish, qattiqlashtirish va issiqlik bilan ishlov berish bilan qiziqasizmi? Yetkazib beruvchi Evek GmbH ishlab chiqaruvchining narxida guruch sotib olishni taklif qiladi. Biz mahsulotlarni qit'aning istalgan nuqtasiga yetkazib berishni ta'minlaymiz. Narx optimal. Sizni hamkorlikka taklif qilamiz.
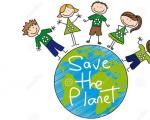