Logistica de producție Condiții preliminare pentru logistica de producție o o. Productie
LogisticăAydin Elena Valerievna Subiectul #3:
„Producție
logistică" CONȚINUT TEMA #3:
Esența logisticii de producție.
Concepte de organizare a managementului producției.
Funcțiile logisticii de producție.
Model în formă de pâlnie al unui sistem logistic.
Reguli de priorități în îndeplinirea comenzilor.
Sisteme de control push and pull.
Managementul si planificarea organizatiei
fluxuri de materiale (producție). Fluxul de material pe drumul său de la primar
sursa de materii prime trece la consumatorul final
un număr de unități de producție.
Managementul fluxului de materiale în această etapă are propriile sale
specificitate și se numește logistică de producție.
LOGISTICĂ DE PRODUCȚIE (PL) –
Acesta este un subsistem al sistemului logistic al întreprinderii,
în cadrul căruia gestionarea materialelor şi
fluxurile de informații pe drum de la depozitul de materiale
resurse către depozit produse finite. Productie
logistica reprezintă reglementare
procesul de producție în spațiu și timp.
SCOPUL LOGISTICII DE PRODUCȚIE:
Sincronizează cu precizie procesul de producție și
operațiuni logistice în interconectate
divizii ale întreprinderii Se numesc sisteme logistice considerate de logistica de productie, precum si obiectul studiului acesteia
sisteme logistice intra-producție (ILS).
Acestea includ: întreprindere industrială; întreprindere en-gros, având dotări de depozitare; butuc de marfă;
nodal port etc.
La nivel macro, intra-producție sisteme logistice acţionează ca elemente ale sistemelor macrologistice. Ei întreabă
ritmul de funcţionare al acestor sisteme sunt surse fluxurile de materiale.
La nivel micro, sisteme logistice intra-producție
reprezintă un număr de subsisteme care se află în relații și conexiuni
unul cu celălalt, formând o anumită integritate, unitate. Aceste subsisteme (achizitii, depozite, stocuri, servicii de productie, transport,
informații, vânzări și personal) asigură intrarea fluxului de materiale în sistem, trecerea în interiorul acestuia și ieșirea din sistem.
În conformitate cu conceptul de logistică, construcția unei rețele aeriene ar trebui să ofere posibilitatea de coordonare constantă și ajustare reciprocă
planuri si actiuni ale unitatilor de aprovizionare, productie si vanzare
în cadrul întreprinderii, adică oferte de logistica de productie
sunt integrate planificarea operațională și managementul fluxului de materiale în producție. Acceptare decizii de managementîn logistica producţiei
efectuate pe baza datelor privind progresul producției
comenzi, informații despre resurse și cererea consumatorilor.
DURATA CICLULUI COMANDĂ
Durată
producție
ciclu
Preţ
Informații despre progres
onorarea comenzii
Posibilitati
de cooperare
furnituri
Informații despre
resurse
Furnizori
Sortiment și
nomenclatură
comenzi
Controla
material
cursuri
Termenele limită
livrare
Nou
comenzi
Informații despre
consumator
la cerere
Informații despre
cererea consumatorilor SISTEM DE CONTROL
FUXURI DE MATERIALE
Informații despre
resurse
Organ
management
Planuri, decizii,
corective
impact
Informații despre
progres
comenzi
Gata
produse
Materii prime
Piaţă
furnituri
Informații despre
consumator
la cerere
Obiect
management
Piaţă
vânzări CONCEPTE LOGISTICE
ORGANIZAȚII DE PRODUCȚIE
Conceptul logistic (acceptabil pentru condițiile „piață a cumpărătorului”)
organizarea producției include următoarele prevederi de bază:
realizarea unui grad ridicat de integrare în cadrul întreprinderii şi între aceasta
furnizori și consumatori;
creșterea flexibilității și adaptabilității producției la condițiile pieței;
eliminarea stocurilor în exces;
refuzul timpului umflat pentru efectuarea operațiunilor de bază și de transport și depozit;
refuzul de a fabrica serii de piese pentru care nu exista comanda clientului;
eliminarea timpilor de nefuncţionare a echipamentelor;
eliminarea obligatorie a defectelor;
eliminarea transportului irațional în interiorul fabricii.
Concept tradițional (acceptabil pentru o „piață a vânzătorului”)
organizarea productiei presupune:
nu opriți niciodată echipamentul principal și întrețineți-l indiferent de situație
indiferent ce coeficient ridicat utilizarea acestuia;
produce produse în loturi cât mai mari posibil;
au maxim stoc mare resurse materiale"doar în cazul în care"
întâmplarea”. FUNCȚII DE PRODUCȚIE
LOGISTICĂ
1. Coordonarea acțiunilor participanților la procesul logistic constă în formularea și aducerea obiectivelor managementului fluxului de materiale către diviziuni individuale, în coordonare a obiectivelor enunţate cu obiectivele globale ale întreprinderii şi
asigurarea pe această bază a lucrului comun coordonat al tuturor părților logisticii
lanţuri.
2. Organizarea fluxurilor materiale în producţie presupune formarea şi
stabilirea de conexiuni spațiale și temporale între participanți
circulaţia mărfurilor, precum şi crearea unui sistem de management al fluxului de materiale pentru
întreprindere.
3. Planificarea fluxurilor de materiale include implementarea unor astfel de subfuncții,
ca științifice, tehnice și prognoza economica, dezvoltarea programului
acțiuni și planuri detaliate. Astfel, îndeplinește sarcina de a estima
tendinţele viitoare în starea sistemului logistic intra-producţie.
În funcție de obiective, previziunile în managementul materialelor pot fi
împărțit în următoarele grupe:
previziuni de dezvoltare tehnică, al căror scop este prognoza în domeniu
modalități de a crea noi tipuri de produse și schimbări în tehnologia de producție,
apariția de noi materiale;
previziuni ale cererii de produse în vederea înlocuirii produselor fabricate cu altele noi sau
reducerea volumului producției sale, identificarea tendințelor de aprofundare a diversificării
producție;
previziuni ale resurselor materiale care vizează determinarea nevoii de
materiale ținând cont de posibilele schimbări în politica de produse a întreprinderii;
se întocmesc previziuni pentru modificarea prețurilor la materiale pentru a crea stocuri ale acestora
tipuri de materiale, este posibil ca prețurile să crească. FUNCȚII DE PRODUCȚIE
LOGISTICĂ
4. Monitorizarea evoluției procesului de distribuție a mărfurilor în cadrul sistemului logistic intra-producție, ca funcție de management
fluxurile de materiale se realizează prin canale determinate
structura organizatorica a intreprinderii, si consta in continuu
monitorizarea derulării procesului de distribuție a mărfurilor conform stabilit
parametrii. În acest scop, informațiile sunt colectate și prelucrate
despre starea fluxurilor de materiale sunt identificate și analizate
abateri de la obiectivele planificate pentru implementarea productiei
comenzi, se trag concluzii cu privire la gradul de conformitate a muncii prestate
sarcini atribuite.
5. Reglementarea evoluției lucrărilor efectuate include următoarele operațiuni: analiza încălcărilor programului de lucru pentru executarea comenzilor de producție și a motivelor care le-au determinat, elaborarea unui program de eliminare a abaterilor și măsuri pentru asigurarea implementării acestuia. MANAGEMENTUL MATERIALELOR
FLUXURI ÎN CADRUL SISTEMELOR LOGISTICE DE INTERPRODUCTIE
MODEL DE PÂLNIE
SISTEM LOGISTIC
Gestionarea mișcării fluxurilor de materiale în
producția poate fi realizată folosind
modele de pâlnie. „Pâlnie” servește pentru simplificare
descrieri ale procesului de deplasare a fluxurilor de materiale în
link-uri individuale lanț de aprovizionare.
Obiectul real al modelului poate fi: atelier,
complot, locul de munca, depozit sau sistem de transport
sistem. Primirea comenzilor
Comenzi în
prelucrare
Maxim
punct de control
abilitate
Eliminarea comenzilor
Intensitatea muncii
munca, ora
MODEL DE PÂLNIE
SISTEM LOGISTIC
Lansa
Durată
buclă de execuție
comanda
Neterminat
producție
Emisiune
Perioada de studiu
Timp EXPLICAȚII PENTRU GRAF (FIGURA)
Ordinele care intră în pâlnie sunt reprezentate ca bile
de diferite dimensiuni. Volumul mingii corespunde intensității travaliului
comanda. Sistemul are debit maxim
(puterea), care se realizează sub rezerva raționalului
planificarea fluxurilor de materiale (repartizarea comenzilor conform
segmente ale perioadei de planificare și formarea priorității
efectuarea muncii). Procesul de primire și eliminare a comenzilor
descris ca o linie întreruptă „lansare” sau „lansare”.
Durata medie a ciclului comenzii
se stabileşte pe baza volumului de lucru în curs şi
debitul real al sistemului conform formulei:
Unde
T avg. c – durata medie a ciclului de onorare a comenzii;
NP av – valoarea medie a lucrărilor în curs;
N avg – numărul mediu de comenzi finalizate
pe unitatea de timp. REGULI DE PRIORITATE IN
EXECUTAREA COMENZILOR
Reguli prioritare pentru reducerea timpilor de așteptare și
Durata medie a ciclului de onorare a comenzii este:
FIFO: „primul intrat, primul ieşit”, adică cea mai mare prioritate
atribuit comenzii care a intrat în sistem mai devreme decât altele;
LIFO: „ultimul intrat, primul ieşit”, adică cel mai înalt
Se acordă prioritate comenzii primite cel mai recent pentru service.
Această regulă este folosită cel mai adesea în sistemele de stocare în acelea
cazurile în care materialele sunt dispuse astfel încât să poată fi atinse
numai de sus;
SPT: „regulă de operare cea mai scurtă”, cea mai mare prioritate este acordată comenzii cu cel mai scurt timp de execuție într-o anumită legătură.
În cazurile în care scopul managementului fluxului de materiale este de a asigura termene de livrare stabilite, se folosesc regulile
controale care iau în considerare informații despre timpii de onorare a comenzilor;
MST: „Timp minim de slăbire”, cea mai mare prioritate este acordată comenzii cu cel mai mic timp de slăbire. Rezervare timp -
este diferența dintre data de finalizare a comenzii și data limită a comenzii
poate fi efectuată în absența urmăririi interoperative;
EDD: „cea mai devreme dată scadentă”, adică cea mai mare prioritate
atribuite comenzii cu cea mai devreme dată de finalizare. METODE DE CONTROL
CURSUL DE MATERIALE IN
ÎN CADRUL IN-PRODUCȚIEI
SISTEME LOGISTICE
Managementul materialelor în cadrul
sistemele logistice intra-producţie pot
realizat de două fundamental diferite
moduri: prin „împingere” sau „tragere”
comanda.
Astfel:
prima metodă este „sistemul push-out”
(„sistem push”);
a doua metodă este „sistemul de tragere”
(„sistem de tragere”) SISTEM DE IMPINGERE
(SISTEMUL PUSH)
Sistem de management al materialelor „Push”.
bazată pe prognoza mărimii stocurilor de materii prime, materiale,
piese pentru fiecare verigă din lanțul de aprovizionare. Pe baza acestei prognoze, este gestionat întregul proces în mai multe etape
producţie prin asigurarea unui volum justificat de material
stoc în fiecare etapă de prelucrare.
Cu acest sistem de management al fluxului de materiale, obiectele de muncă sunt mutate dintr-o zonă în alta (următoarea
proces tehnologic) indiferent de disponibilitatea lui pentru prelucrare
și cerințele pentru aceste părți, de ex. fără o comandă corespunzătoare. Fluxul de material este „împins” către destinatar la comandă,
provenind din sistemul central de control al producţiei.
Această metodă de gestionare a fluxurilor de materiale permite
lega un mecanism complex de producție în sistem unificatŞi
să maximizeze utilizarea lucrătorilor și a echipamentelor în producție.
Cu toate acestea, în cazul unei schimbări bruște a cererii, utilizarea unui sistem „push” duce la crearea de inventar în exces și
„supra stocare” din cauza lipsei posibilității de reprogramare”
producție pentru fiecare etapă. SISTEM DE IMPINGERE
(SISTEMUL PUSH)
Modelele de control al debitului „push” sunt tipice pentru tradiționale
noi metode de organizare a producţiei, pentru întreprinderile de achiziţii şi
întreprinderile producătoare de produse standardizate.
În practică, au fost implementate diverse opțiuni pentru sistemele de „împingere”.
Acestea includ concepte RP (MRP - discutat în prelegerea nr. 1).
Sistem central
Controlul clasei RP
Depozit
materii prime
Atelierul nr. 1
...
Atelierul Nr.n
Depozitul terminat
produse
Fluxul materialului
Fluxul de informații SISTEM DE TRAGERE
(SISTEM DE TRAGERE)
Sistemul „pull” presupune menținerea unui nivel minim de stoc la fiecare etapă a producției și mișcării comenzii
de la secțiunea următoare la cea anterioară. Secțiunea ulterioară
comandă material în conformitate cu norma și timpul de consum al produselor sale.
Aici sistemul de control central nu interferează cu schimbul
fluxurile de materiale între diferite zone
întreprinderilor, nu stabilește standardele actuale de producție pentru acestea
sarcini. Program de producție a unui tehnologic separat
link-ul este determinat de dimensiunea comenzii link-ului următor.
Sistemul de control central stabilește sarcina numai pentru
veriga finală a lanțului procesului de producție. Proces
are loc în direcția opusă mișcării materialului
curgere.
Astfel, cu acest sistem, doar acelea
detalii care sunt cu adevărat necesare și numai atunci când este necesar
apare o nevoie. SISTEM DE TRAGERE
(SISTEM DE TRAGERE)
Sistemul „pull” se bazează pe conceptul „Just in
termen limită” (JIT). Acest concept este concentrat în primul rând
pentru cerere stabilă, lucrați cu un nivel minim de inventar sau
fără rezerve deloc, ceea ce înseamnă că cu fluctuații semnificative ale valorii
cererea duce la lipsuri și defecțiuni ale sistemului.
Sistem central
Controlul clasei JIT
Depozit
materii prime
Atelierul nr. 1
...
Atelierul Nr.n
Depozitul terminat
produse
Fluxul materialului
Fluxul de informații EXEMPLU DE SISTEM PULL
Să luăm în considerare mecanismul de funcționare al sistemului de tragere
managementul fluxului de materiale. Să presupunem că compania a primit o comandă
pentru productia a 10 unitati. produse. Sistemul de control transmite această comandă atelierului
ansambluri. Atelierul de montaj solicita 10 piese de la magazinul nr. 1 pentru a onora comanda.
După ce a transferat 10 piese din stocul său, atelierul nr. 1 pentru a completa stocul
comandă 10 semifabricate de la atelierul nr.2. În continuare, atelierul nr. 2, după ce au transferat 10 semifabricate,
comandă materiale de la depozitul de materii prime pentru producerea aceluiași număr de semifabricate, tot în scopul refacerii stocului. Astfel,
fluxul de material este „tras” de către fiecare legătură ulterioară.
Depozit
Atelierul nr. 2
Comanda pentru
material
Atelierul nr. 1
Comanda pentru
10 spatii libere
Magazin
ansambluri
Comanda pentru
10 piese
10 unitati
produse
Echipa pentru a produce 10 unități. produse
10
detalii
10
spatii libere
Material
Sistem de control
PIAȚA DE VÂNZĂRI
Comanda pentru 10 unitati. produse SISTEM DE TRAGERE
(SISTEM DE TRAGERE)
Pentru a elimina toate neajunsurile la implementarea conceptului
„La timp”, trebuie îndeplinite cerințe stricte:
stabilirea de lucru coordonat cu furnizorii și consumatorii folosind mijloace moderne comunicații;
aplica metode moderne, tehnologii de producție și echipamente industriale;
să respecte cu strictețe termenele de livrare și nivelurile de calitate;
introduce modern sisteme informatice management.
În practică, la logistica „pull” intra-producție
sistemele includ sistemul „KANBAN” (tradus din japoneză ca card),
dezvoltat și implementat de Toyota (Japonia).
Sistemul KANBAN nu necesită informatizarea totală a producției, dar presupune o disciplină ridicată a aprovizionării, precum și
responsabilitate înaltă a personalului, deoarece reglementarea centralizată a procesului logistic intra-producție este limitată.
Nu există un program strict de producție și toată producția este activată
fiecare loc de munca este construit pe baza comenzii primite
de la locul de muncă ulterior. ORGANIZAREA SI MANAGEMENTUL
FUXURI DE MATERIALE
Organizarea fluxurilor de materiale și managementul acestora
la întreprindere sunt indisolubil legate între ele şi
formează un sistem.
În procesul de organizare se realizează unificarea
se creează fluxuri şi condiţii elementare pentru
funcționarea eficientă a producției
sistem logistic.
Managementul materialelor oferă
monitorizarea constantă a progresului
comenzi de producție și asigură necesarul
impact asupra sistemului logistic pentru a
menține parametrii acestuia în limitele specificate pentru
atingerea obiectivelor stabilite pentru întreprindere. Pentru a caracteriza aspectul temporal al organizării materialelor
streams sunt utilizate următoarele concepte:
- ciclul de onorare a comenzii este complex într-un anumit fel
fluxuri elementare organizate în timp care apar când
efectuarea de operatiuni logistice in procesul de promovare a comenzii cu
momentul primirii acestuia până la executare;
- momentul primirii comenzii caracterizeaza momentul primirii
cerere pentru fabricarea de produse de un anumit tip și scop;
- momentul finalizării comenzii înseamnă că produsul ajunge la punctul de vânzare cu amănuntul
rețea – pentru bunuri de consum personal sau către depozitul întreprinderii clientului
– pentru produse de uz industrial;
- durata ciclului comenzii este perioada calendaristică în care
sunt efectuate toate operațiunile pentru finalizarea comenzii și se calculează următoarele:
Unde
Tooz – timpul pentru procesarea și plasarea unei comenzi;
Ttp – timp de pregătire tehnică;
Tz – timpul de procurare a materialelor;
Тпз – timpul de pregătire pentru lansare;
Tpts – durata ciclului de producție;
Тп – timpul de livrare;
Tper – timpul întreruperilor apărute din cauza
asincronia etapelor individuale ale ciclului. EXEMPLU FORMALIZAT DE STRUCTURĂ
CICLU DE FINALIZARE COMANDA PENTRU PLUS
Etapele ciclului
Primirea unei comenzi
Tehnic
Pregătirea
Livra
materiale
Pregătirea
a lansa
Fabricarea
comanda
Livra
comanda
Grupuri de operare
Contabilitate, procesare si comanda
Dezvoltarea tehnologiei de proiectare și fabricație
Pregătirea organizatorică
Dezvoltare
Organizarea tranziției către lansarea unui nou produs
Formarea unui ordin
Selectarea furnizorilor
Primirea si depunerea materialelor in depozit
Primirea spațiilor libere
Alegerea echipamentelor tehnologice necesare
Efectuarea sincronizării preliminare P
Elaborarea unui program de lansare a produsului
Operatii tehnologice
Controlul tehnologic al producției
Transport
Expediere
Depozitarea produselor finite
Finalizarea comenzii
Livrarea comenzii către consumator Totalitate mijloace tehnice, care creează oportunitatea
fluxul de materiale și amplasarea zonelor de producție și a depozitelor
(acționări) în raport cu acesta, exprimat printr-un sistem de stabil
conexiuni, este o formă de organizare a mișcării materialelor
cursuri.
FORME DE ORGANIZARE PENTRU MIȘCAREA MATERIALELOR:
1. Forma cumulativă de organizare se caracterizează prin faptul că pt
funcţionarea normală a sistemelor logistice în componenţa lor prevede
complex de depozite.
Acestea includ: depozite de metal și țagle; depozite de piese inter-site,
unități și componente; depozite de produse finite; magazii
echipamente tehnologice. Materialul se îndepărtează de depozit
metale și semifabricate prin depozite intermediare până la locurile de producție și
apoi la depozitul de produse finite.
Avantajul acestei forme este posibilitatea de a acumula un mare
volumul de material la intrarea și la ieșirea sistemului, ceea ce asigură, pe de o parte,
fiabilitatea primirii pieselor necesare, semifabricatelor, componentelor in
productia, in schimb, garanteaza indeplinirea solicitarilor urgente
consumatorii de produse.
Dezavantajul formei cumulate de mișcare a materialelor este că
prezenţa unui sistem extins de rute de transport şi a unui număr mare de depozite
face dificilă gestionarea mișcării fluxurilor de materiale și controlul stocurilor.
În plus, costurile asociate cu imobilizarea fondurilor în
materiale și necesitate investitii de capital pentru a crea un sistem
depozite FORME DE ORGANIZARE
2. Forma transport-cumulativă a organizaţiei presupune prezenţa
sistem combinat de transport și depozitare (TCS), care unește un anumit număr de locuri de muncă (zone) prin stabilirea unei comunicări între fiecare lucrător
loc (site) cu oricare altul prin informații și materiale
cursuri.
În același timp, procesele de prelucrare (asamblare), control, pregătire a producției, depozitare și reglare a materialelor sunt combinate folosind TSS într-un singur proces de producție. Mișcarea fluxului de material este controlată
conform schemei: căutarea piesei necesare în depozit - transport la mașină - prelucrare - returnarea piesei la depozit. Acumularea de material se realizează în
depozit central sau descentralizat către zonele individuale de lucru.
În primul caz, depozitul deservește mai multe departamente de producție și
utilizat ca dispozitiv de stocare de rezervă între începutul și sfârșitul procesării piesei. În al doilea caz, depozitele sunt create în zone separate și servesc la compensarea abaterilor de timp în timpul transportului și procesării piesei. În unele cazuri, se folosește un TSS mixt, care presupune prezența atât a unui depozit central, cât și a unor spații de depozitare de rezervă în zonele de lucru.
Avantajele acestei forme sunt: reducerea volumului de stocuri pentru muncitori
localități prin crearea TSS; reducerea timpului procesului de producție
prin eliminarea pauzelor între componentele ciclului de producție; control constant asupra stocurilor; prezența unui sistem de management bine organizat
mișcarea materialelor.
Dezavantaje: forma de transport-depozitare este eficientă pentru grupuri de piese omogene din punct de vedere structural și tehnologic, care, în primul rând, își îngustează aria
aplicarea, în al doilea rând, necesită un complex munca pregatitoare; această formă cere investiții semnificativeîn creaţie sistem automatizat managementul progresului producției. FORME DE ORGANIZARE
3. Forma de organizare a stocului zero presupune crearea de consolidate
bucle de control bazate pe unități de producție autonome autonome. Miezul circuitului este conectarea unui depozit tampon (depozitare).
zone de producție separate între ele. Fiecare dintre secțiuni poate contacta oricare alta prin intermediul unității corespunzătoare. Caracteristică
bucla de control integrată este formarea orizontalei
conexiuni de-a lungul întregului lanț tehnologic, ceea ce permite legături de producție
interacționează în mod independent și direct unul cu celălalt.
Lansarea pieselor în producție și prelucrarea lor se efectuează în cantități mici
în loturi conform comenzii primite. După terminarea execuției
operațiuni în cadrul unui modul de producție, piesele ajung la depozit și
rămâne acolo până când se primește o cerere de la site-ul următor
prelucrare.
Furnizor de site
COMANDA FINALIZATA
COMANDA DE LIVRARE SI PRODUCERE
Depozitare pliabilă
Zona consumator
COMANDA FINALIZATA
Avantajul acestei forme este posibilitatea utilizării unui sistem de management al fluxului de material extras, care asigură un stoc de producție standard minim.
Dezavantaje: utilizarea sa în întreprinderile autohtone este dificilă din cauza
nivelul scăzut de informatizare a managementului producţiei şi lipsa de
sistem durabil de aprovizionare cu materialele necesare. METODE DE CALCUL DE CĂLĂTORII PLANIFICATE
PRODUCȚIE CU OPERAȚIONAL
PLANIFICARE:
Metodă
Conţinut
Conceput pentru a determina date specifice de producție
producția (lansare, lansare de produs etc.) a fiecărui articol
metodă
produse planificate. Metoda calendarului se bazează pe
nia (analog cu determinarea ciclului de producție al unui produs și este utilizat
să formuleze un program lunar de producţie.
MRP I)
Asigură coordonarea simultană a termenelor și volumelor
a muncii efectuate în sistemul de producţie cu posibil
Volumetric debitului unități de producție în
calendarul în ansamblu pentru întreaga perioadă de timp luată în considerare. OKM
metodă
însoțită de calcule ale ciclului de producție al produsului și
sarcina planificată a fiecărei unități de producție pe tip
lucrări de cercetare (OKM).
Şi
se aplică
la
formare
menstruaţie
programe de producție.
OCM este utilizat în mod tradițional în sistemele MRP II.
Este cea mai avansată dintre serialele luate în considerare.
Volumetric Vă permite să luați în considerare simultan sincronizarea, volumul și dinamica
producerea dinamică a muncii în conformitate cu metoda nomenk planificată
rata de eliberare și să utilizeze mai deplin instalațiile de producție existente (ODM)
resurse venoase.
Vă puteți familiariza cu această metodă în detaliu în lucrări
Yu.Yu. Naimarka.
logistică
Condiții preliminare pentru logistica producției
Volatilitatea și imprevizibilitatea cererii pieței fac imposibilă crearea și menținerea stocurilor.
În același timp, producătorul nu are dreptul să rateze o singură comandă, de unde necesitatea unor facilități de producție flexibile, care să poată răspunde rapid cererii emergente.
Necesitatea de a asigura competitivitatea produselor sale într-o situație de piață este deosebit de acută pentru fiecare unitate de afaceri.
Scopul logisticii de producție
Organizarea managementului fluxurilor de materiale si informatii in cadrul sistemului logistic si in cadrul procesului de productie
Optimizarea fluxurilor de materiale în cadrul întreprinderilor care creează bunuri materiale sau prestează servicii materiale, evitând eșecurile de producție.
O trăsătură caracteristică a obiectelor de studiu în logistica producției este compactitatea lor teritorială.
Asigură că fluxul de material intră în sistem, trece prin acesta și iese în următoarele subsisteme
Sistemele logistice de producție combină fluxurile de materiale și stabilesc ritmul de lucru pentru toate celelalte subsisteme, determinând posibilitățile de adaptare la schimbările de mediu.
Abordarea logistică a organizării producției include:
eliminarea stocurilor în exces;
refuzul timpului umflat pentru efectuarea operațiunilor de bază și de transport și depozit;
refuzul de a fabrica serii de piese pentru care nu exista comanda clientului;
eliminarea timpilor de nefuncţionare a echipamentelor;
eliminarea obligatorie a defectelor;
eliminarea transportului irațional în interiorul producției;
transformarea furnizorilor din părțile opuse în parteneri binevoitori.
Managementul fluxului de materiale în cadrul sistemelor logistice de producție poate fi realizat în două moduri:
1) folosind un „sistem push”
2) folosind un „sistem de tragere”
Sistem de împingere
Obiecte de muncă furnizate către loc de producție, direct prin această secțiune din linkul tehnologic anterior nu sunt comandate.
Fluxul de material este „împins” către destinatar la comanda sistemului central de management al producției.
Principalul dezavantaj al sistemelor push este asociat cu necesitatea creării și menținerii unor stocuri tampon semnificative între unitățile de producție și etapele ciclului tehnologic.
Apăsați opțiunile sistemului
MRP (Material Requirement Planning) este o organizație general acceptată de ideologie, tehnologie și management întreprinderile industriale
Sistemul MRP implementează următoarele funcții principale:
reglementarea actuală și controlul stocurilor industriale;
în timp real, coordonează și ajustează cu promptitudine planurile și acțiunile diferitelor servicii ale întreprinderii - aprovizionare, producție, vânzări.
Parametrii fluxului de material „împins” spre șantier sunt optimi în măsura în care sistemul de control este capabil să țină cont și să evalueze toți factorii care influențează situația producției la acest șantier.
Cu cât sistemul de control trebuie să ia în considerare mai mulți factori pentru fiecare dintre numeroasele secțiuni ale întreprinderii, cu atât software-ul, informațiile și suportul tehnic ar trebui să fie mai avansate și mai scumpe.
Descrierea prezentării prin diapozitive individuale:
1 tobogan
Descriere slide:
Subiectul 2.4 Logistica de productie O serie de prelegeri susținute de profesorul Lamtev N.V. Subiectul 2.4. Logistica de fabricație
2 tobogan
Descriere slide:
Condiții Logistica producției - reglementarea procesului de producție în spațiu și timp, respectiv planificarea și gestionarea fluxurilor de materiale, organizarea transportului intra-producție, stocarea (depozitarea) și menținerea stocurilor (întârzieri) de materii prime, materiale și lucrări în curs procesele de productie la etapele de procurare, prelucrare si asamblare a produselor finite. 25.02.2014 Subiectul 2.4. Logistica producției * Subiectul 2.4. Logistica de fabricație
3 slide
Descriere slide:
Condiții Scopul logisticii de producție este de a optimiza fluxurile de materiale în cadrul întreprinderii. Managementul Materialelor - Proces impact vizat către unitățile de producție angajate în promovarea fluxurilor materiale și informaționale de la punctul de producție până la punctul de consum al produselor. 25.02.2014 Subiectul 2.4. Logistica producției * Subiectul 2.4. Logistica de fabricatie NATA - null
4 slide
Descriere slide:
Obiectivele logisticii de producție: asigurarea producției de înaltă calitate, la timp și completă a produselor; reducerea ciclului de producție; raţionalizarea costurilor de producţie.
5 slide
Descriere slide:
Instrumente de planificare a logisticii producției, organizarea fluxului de materiale, management operațional 25.02.2014 Tema 2.4. Logistica de fabricație * Subiectul 2.4. Logistica de fabricație
6 diapozitiv
Descriere slide:
Exemple de sisteme logistice de producție: întreprindere industrială; întreprindere cu ridicata; hub de marfă; port maritim etc.
7 slide
Descriere slide:
Ciclul de producție: perioada de timp dintre începutul și sfârșitul procesului de producție în raport cu produse specificeîn cadrul sistemului logistic, ciclul de producție al unui produs este un set ordonat al tuturor proceselor prin care un produs trece de la începutul până la sfârșitul fabricării sale.
8 slide
Descriere slide:
Principiile procesului de producție Principiul continuității producției; Principiul producției proporționale. Principiul paralelismului și fluxului direct al producției
Slide 9
Descriere slide:
Durata ciclului de producție al unui produs este perioada calendaristică de la începutul până la sfârșitul producției produsului în ansamblu, incluzând toate componentele acestuia. 25.02.2014 Subiectul 2.4. Logistica de fabricație * Metode de organizare a procesului de producție în timp, caracteristicile și condițiile de utilizare ale acestora Tema 2.4. Logistica de fabricație
10 diapozitive
Descriere slide:
Metode de organizare a procesului de producție în timp, caracteristicile și condițiile de utilizare a acestora Un lot de produse este un grup de produse identice lansate simultan în procesul de producție. Vom lua în considerare diverse moduri organizarea în timp a procesului de fabricaţie a unui lot de produse. Durata ciclului de operare pentru fabricarea produselor este perioada de timp de la momentul începerii până la momentul finalizării producției unui lot de produse într-o singură operațiune tehnologică. 25.02.2014 Subiectul 2.4. Logistica producției * Subiectul 2.4. Logistica de fabricație
11 diapozitiv
Descriere slide:
Metode de organizare a procesului de producție în timp, caracteristicile și condițiile de utilizare a acestora Durata unui ciclu multioperațional pentru producerea unui lot de produse este perioada de timp de la începutul până la sfârșitul producției unui lot de produse. produse pentru un set dat de operațiuni. Tipuri de organizare a unui ciclu de operațiuni multiple în timp: secvenţial; paralel; serie paralelă. 25.02.2014 Subiectul 2.4. Logistica producției * Subiectul 2.4. Logistica de fabricație
12 slide
Descriere slide:
Tipuri de mișcare a fluxului de material în ciclul de producție: Secvențial - un ciclu cu mai multe operațiuni pentru fabricarea unui lot de produse, în care fiecare operație ulterioară a ciclului începe numai după prelucrarea completă a întregului lot în operația anterioară. Avantaje: fara intreruperi in munca lucratorilor si a echipamentelor in toate operatiunile; simplitatea organizării. Dezavantaje: termen de valabilitate lung și volum mare de lucru în curs; durată semnificativă din cauza lipsei de paralelism în prelucrarea produselor. 25.02.2014 Subiectul 2.4. Logistica producției * Subiectul 2.4. Logistica de fabricație
Slide 13
Descriere slide:
Tipuri de mișcare a fluxului de material în ciclul de producție: Paralel - o metodă de organizare a unui ciclu multi-operațional în care procesarea fiecărui lot de transfer într-o operațiune ulterioară începe imediat după finalizarea operațiunii anterioare. Echipamentul funcționează continuu în timpul celei mai lungi funcții (principale). Structura unui astfel de ciclu este un set ordonat de cicluri operaționale pentru procesarea loturilor de transfer, suprapuse cât mai mult posibil în timp la fiecare pereche de operații adiacente. Un ciclu paralel de operațiuni multiple se caracterizează prin faptul că fiecare parte a unui lot este supusă unei procesări continue în toate operațiunile. 25.02.2014 Subiectul 2.4. Logistica producției * Subiectul 2.4. Logistica de fabricație
Slide 14
Descriere slide:
Avantaje: durata minimă a unui ciclu de operații multiple; nu exista depozitare intraoperationala, produsele se afla doar la prima operatie, asteptand ordinea procesarii lor, iar la ultima, asteptand livrarea lor; ritm pronunțat al procesului. Dezavantaje: întreruperi în funcționarea echipamentelor în toate operațiunile cu excepția celei principale, aceasta determină o scădere a eficienței echipamentelor și a lucrătorilor (întreaga zonă este ocupată cu dificultate în planificarea și coordonarea operațiunilor tehnologice aferente). prelucrarea pieselor relativ scumpe cu o durată lungă de operare, precum și a liniilor de producție continuu unde operațiunile sunt bine sincronizate (ideal toate sunt egale). 25.02.2014 Subiectul 2.4. Logistica de fabricație * Tipuri de flux de materiale în ciclul de producție: Tema 2.4. Logistica de fabricație
15 slide
Descriere slide:
Tipuri de mișcare a fluxului de material în ciclul de producție: Procedura de construire a unui program este un program pentru prelucrarea continuă a primei părți a unui lot în toate operațiunile; se determină operația principală, adică. operațiune cu cel mai înalt standard de timp (în exemplu, aceasta este a 2-a operațiune), se stabilește secvența prelucrării continue a părților rămase ale lotului în operația principală, pe baza programului construit pentru prelucrarea pieselor lotului în principal operațiunea, programele de procesare pentru părțile rămase ale lotului sunt finalizate pentru toate operațiunile, cu excepția operațiunii principale. 25.02.2014 Subiectul 2.4. Logistica producției * Subiectul 2.4. Logistica de fabricație
16 diapozitiv
Descriere slide:
Tipuri de mișcare a fluxului de material în ciclul de producție: Paralel-secvențial - o metodă de organizare a unui ciclu multi-operațional în care transferul fiecărui lot de transfer la operațiunea ulterioară se efectuează la finalizarea prelucrării sale în operația anterioară. Echipamentul funcționează continuu în timpul fiecărei operațiuni. Structura unui astfel de ciclu este structura unui ciclu secvenţial, în care programele de procesare pentru un lot de produse din fiecare pereche de operaţii adiacente se suprapun cât mai mult posibil în timp. 25.02.2014 Subiectul 2.4. Logistica producției * Subiectul 2.4. Logistica de fabricație
Slide 17
Descriere slide:
Tipuri de deplasare a fluxului de materiale în ciclul de producție: Avantaje: eliminarea întreruperilor în funcționarea echipamentelor în toate operațiunile cu excepția celei principale, aceasta determină o scădere a eficienței echipamentelor și a lucrătorilor (întreaga zonă este ocupată); nici o urmărire intraoperațională a produselor se află doar în prima operațiune, în așteptarea ordinii procesării lor și pe ultima în așteptarea livrării lor; ritm pronunțat al procesului. Dezavantaje: durata crescută a ciclului de operații multiple; complexitatea planificării și coordonării activității operațiunilor tehnologice conexe 25.02.2014 Subiectul 2.4. Logistica producției * Subiectul 2.4. Logistica de fabricație
18 slide
Descriere slide:
Slide 19
Descriere slide:
Tipuri de productie: la comanda; seriale (la scară mică, în serie și la scară mare); masiv.
20 de diapozitive
Descriere slide:
Direcții de dezvoltare a proceselor tehnologice: îmbunătățirea (creșterea productivității) operațiunilor individuale; raţionalizarea mişcării fluxului de material.
21 de diapozitive
Descriere slide:
Elemente ale conceptului logistic de organizare a producției: respingerea stocurilor în exces; refuzul timpului umflat pentru efectuarea operațiunilor de bază și de transport și depozit; refuzul de a fabrica serii de piese pentru care nu exista comanda clientului; eliminarea timpilor de nefuncţionare a echipamentelor; eliminarea obligatorie a defectelor; eliminarea transportului irațional în interiorul producției; transformarea furnizorilor din părțile opuse în parteneri binevoitori.
22 slide
Descriere slide:
Principii tradiționale și logistice ale managementului producției: volumul maxim posibil „pentru orice eventualitate”; permițând creșterea timpilor ciclului de producție dacă acest lucru reduce costurile de producție; minimizarea gamei de produse fabricate; eliberare în cantități cât mai mari; timpul de nefuncționare a echipamentelor este minimizat și în mod ideal evitat; eliminarea stocurilor în exces; evitând creșterea timpului ciclului de producție dacă aceasta duce la o scădere eficienta economica; stabilirea nomenclaturii în conformitate cu comenzile acceptate; refuzul de a lansa produse care nu sunt confirmate prin comenzi; nivelul de oprire este planificat pentru a crea rezerve de capacitate;
Slide 23
Descriere slide:
Principii tradiționale și logistice ale managementului producției: este permis un nivel de defecte justificat tehnologic; transportul intra-fabrică se efectuează în conformitate cu organizarea acceptată a procesului de producție; calificările sunt sporite în limite înguste, cu scopul de a asigura productivitatea operațională maximă. căsătoria este inacceptabilă dacă poate duce la o scădere a eficienței economice; Transportul irațional intra-fabrică este eliminat, procesul de producție este reorganizat; calificările sunt extinse, cu scopul final de universalizare pentru a asigura o flexibilitate de producție de înaltă calitate.
24 slide
Descriere slide:
Flexibilitatea sistemului de producție și logistică: flexibilitatea sistemului de mașini (durata și costul tranziției la producția următoarei piese); flexibilitatea sortimentului (capacitatea de a actualiza produsele, costul pregătirii producției unui nou tip de piesă); flexibilitate tehnologică (utilizarea diferitelor opțiuni proces tehnologic pentru a netezi eventualele abateri de la programul de producție pre-elaborat); flexibilitatea volumelor de producție (capacitatea de a produce rațional piese în condiții de dimensiuni dinamice ale lotului de lansare, dimensiunea minimă a lotului la care funcționarea sistemului devine oportună); flexibilitatea extinderii sistemului (posibilitatea extinderii în continuare a sistemului).
25 diapozitiv
Descriere slide:
Ideea principală lean manufacturing: Dacă o activitate, operațiune sau proces nu adaugă valoare produsului din punctul de vedere al clientului, atunci acea activitate, operațiune sau proces este considerată deșeu (muda).
26 slide
Descriere slide:
Slide 27
Descriere slide:
Tipuri de pierderi de al doilea fel: supraproducție; inventar în exces; căsătorie; operațiuni și mișcări inutile la locul de muncă; supraprocesare; timp de nefuncţionare; mișcări inutile; pierderea creativității în rândul angajaților
28 slide
Descriere slide:
Noi principii de producție de tip: munca în echipă; schimb deschis intens de informații; utilizare eficientă resurse și eliminarea pierderilor; perfecţionare continuă (kaizen).
Condiții preliminare pentru logistica producției o o o Volatilitatea și imprevizibilitatea cererii pieței fac imposibilă crearea și menținerea stocurilor. În același timp, producătorul nu are dreptul să rateze o singură comandă, de unde necesitatea unor facilități de producție flexibile, care să poată răspunde rapid cererii emergente. Necesitatea de a asigura competitivitatea produselor sale într-o situație de piață este deosebit de acută pentru fiecare unitate de afaceri.
Logistica de producție este o asigurarea unei producții de înaltă calitate, la timp și completă a produselor în conformitate cu contractele de afaceri, reducerea ciclului de producție și optimizarea costurilor de producție
Scopul logisticii producţiei o o Organizarea managementului fluxurilor materiale şi informaţionale în cadrul sistemului logistic şi în cadrul procesului de producţie Optimizarea fluxurilor de materiale în cadrul întreprinderilor care creează bunuri materiale sau prestează servicii materiale, evitând eşecurile producţiei.
o o o Trăsătură caracteristică obiecte de studiu în logistica producţiei şi compactitatea teritorială a acestora. Asigură intrarea fluxului de materiale în sistem, trecerea în cadrul acestuia și ieșirea către următoarele subsisteme. Sistemele logistice de producție combină fluxurile de materiale și stabilesc ritmul de lucru pentru toate celelalte subsisteme, determină posibilitățile de adaptare la schimbările de mediu.
Abordarea logistică a organizării producției include: o o o o respingerea stocurilor în exces; refuzul timpului umflat pentru efectuarea operațiunilor de bază și de transport și depozit; refuzul de a fabrica serii de piese pentru care nu exista comanda clientului; eliminarea timpilor de nefuncţionare a echipamentelor; eliminarea obligatorie a defectelor; eliminarea transportului irațional în interiorul producției; transformarea furnizorilor din părțile opuse în parteneri binevoitori.
Gestionarea fluxului de materiale în cadrul sistemelor logistice de producție poate fi realizată în două moduri: 1) folosind un „sistem de împingere” 2) folosind un „sistem de tragere”
Sistem de împingere o o o Obiectele de muncă care sosesc la locul de producție nu sunt comandate direct de acest site de la legătura tehnologică anterioară. Fluxul de material este „împins” către destinatar la comanda sistemului central de management al producției. Principalul dezavantaj al sistemelor push este asociat cu necesitatea creării și menținerii unor stocuri tampon semnificative între unitățile de producție și etapele ciclului tehnologic.
Opțiuni pentru sisteme push o o MRP (Material Requirement Planning) este o ideologie general acceptată, tehnologie și organizare a managementului întreprinderilor industriale Sistemul MRP implementează următoarele funcții principale: reglementarea curentă și controlul stocurilor industriale; în timp real, coordonează și ajustează cu promptitudine planurile și acțiunile diferitelor servicii ale întreprinderii - aprovizionare, producție, vânzări.
o o Parametrii fluxului de materiale „împins” în șantier sunt optimi în măsura în care sistemul de control este capabil să țină cont și să evalueze toți factorii care influențează situația producției din acest șantier. Cu cât sistemul de control trebuie să ia în considerare mai mulți factori pentru fiecare dintre numeroasele secțiuni ale întreprinderii, cu atât software-ul, informațiile și suportul tehnic ar trebui să fie mai avansate și mai scumpe.
Sistem de tragere o o Piesele și semifabricatele sunt alimentate la operațiunea tehnologică ulterioară de la cea anterioară în funcție de necesități. Programul de producție al unei legături tehnologice individuale este determinat de dimensiunea comenzii legăturii ulterioare.
o o „Sistem de tragere” . Cu această metodă, sistemul central nu interferează cu schimbul de fluxuri de materiale între diferite părți ale întreprinderii și nu stabilește sarcinile curente de producție pentru acestea. Sistemul de tragere are avantaje față de sistemul de împingere, deoarece personalul magazinului este capabil să ia în considerare mai mulți factori specifici care determină dimensiunea. ordine optimă decât sistemul central de control.
Avantajele sistemului de tragere: o o o eliminarea excesului de stoc, înlocuirea cu informații despre posibilitatea achiziționării rapide a materialelor sau disponibilitatea capacității de rezervă pentru a răspunde rapid la schimbările cererii; înlocuirea politicii de vânzare a mărfurilor manufacturate cu o politică de producere a mărfurilor vândute; sarcina de utilizare a capacitatii maxime, inlocuita cu minimizarea timpului necesar pentru trecerea produselor prin procesul tehnologic; reducerea lotului optim de resurse și a lotului de procesare; reducerea tuturor tipurilor de timpi de nefuncționare și a transportului irositor în interiorul fabricii.
Opțiuni pentru sistemele de tragere o o o KANBAN Principalele avantaje ale sistemului de micro-logistică KANBAN este capacitatea de a asigura buna funcționare a tuturor departamentelor de producție ale companiei, coordonate cu cererea. permite reducerea semnificativă inventarele
Eficacitatea KANBAN este asigurată prin respectarea mai multor reguli: 1) Etapa ulterioară trage produsele necesare din etapa anterioară în cantitatea necesară si la un timp strict stabilit. 2) În zonele de producție de procesare, nicio piesă nu poate fi fabricată până la primirea unui card de producție care autorizează producția 3) Numărul de carduri kanban trebuie să corespundă strict cu numărul de produse 4) Nicio piesă nu este produsă decât dacă există un card de producție 5) Diverse piese trebuie fabricate în ordinea în care au fost primite cardurile 6) Produsele defecte nu trebuie trimise la următoarea secțiune 7) Numărul de carduri trebuie să fie d.b. minim, deoarece reflectă oferta maximă de piese. Dreptul de modificare a numărului de carduri aparține personalului de conducere intermediară. 8) Pentru fiecare container există 1 card de transport și 1 card de producție, numărul de containere este calculat de către managerul de producție 9) Se folosesc numai containere standard care pot găzdui un anumit număr de piese
Dezavantajele sistemului KANBAN o o Nu este eficient în întreprinderile caracterizate prin producție neregulată, durate diferite ale ciclurilor de producție, deoarece poate duce la întreruperi ale muncii, pierderi de productivitate, utilizare insuficientă a capacității de producție și alte consecințe negative ale sistemului disciplină ridicată în aprovizionare, precum și responsabilitate ridicată a personalului.
Sistemul Just-in-Time o o Vă permite să identificați probleme care nu sunt vizibile din cauza stocului în exces și a personalului în exces. Ideea unui sistem este de a produce și livra produse finite exact la timp pentru vânzarea lor. Piese separate în momentul asamblarii unităților. Unități și componente la momentul asamblarii produsului în ansamblu.
Avantajele sistemului JT „Just in Time”: o o o prevede o reducere a dimensiunii loturilor de piese prelucrate; reducerea restanțelor; minimizarea nivelurilor stocurilor
o o o Condiții de utilizare a sistemului „J T”: nivel ridicat de automatizare, sincronizare a proceselor de producție, nivel ridicat de cultură de producție calitate superioară lichidarea produselor de înaltă productivitate facilitati de depozitare aproape imposibil fără o reducere semnificativă a timpului pentru schimbarea echipamentului
Sistem ORT (Optimized Production Technology) - optimizat tehnologie de producție o Este un exemplu de sinteză în producția de elemente cheie ale MRP și KANBAN bazate pe tehnologii informatice și informatice moderne o Aparține clasei de sisteme micrologistice „pull” care integrează procesele de aprovizionare și producție.
o Scopul sistemului ORT este identificarea în producție blocajele sau, în terminologia creatorilor, „resurse critice”, care sunt materii prime, materiale, mașini, echipamente, procese tehnologice și personal.
o o o Efectul sistemului ORT din perspectivă logistică este: reducerea costurilor de producție și transport reducerea stocurilor de lucrări în curs reducerea timpului ciclului de producție reducerea nevoii de depozit și spațiu de producție creșterea ritmului de expediere a produselor finite către consumatori
Sistemul „Șapte 0” o o o o o Modificarea sistemului JIT. Caracteristicile sale: 0 defecte (de înaltă calitate) 0 timpi de nefuncționare (timp minim de configurare la schimbarea unui produs) 0 dimensiunea lotului la locul de muncă 0 pierderi de timp și costuri pentru transport 0 produse în exces 0 timp de nefuncționare la depanare 0 timp de ciclu (total de primele 6 puncte) 0 nu înseamnă reducerea la zero absolut, ci minimizarea, ceea ce ne străduim.
Sistemul TQM (Total Quality Management) o o o este o abordare de management în toate elementele sistemelor logistice, concentrându-se pe sarcina de îmbunătățire a calității bazată pe participarea la rezolvarea acestei probleme a întregii echipe a întreprinderii la etapele de producție și promovare a produselor ( servicii) permițând atingerea succesului pe termen lung prin satisfacerea nevoilor consumatorilor și prin beneficiul reciproc atât al fiecărui membru al întreprinderii, cât și al societății în ansamblu.
o o Flexibilitate - capacitatea sistemelor de producție și logistică de a se adapta rapid la condițiile de operare în schimbare cu costuri minime si fara pierderi. Sistemele flexibile de producție și logistică au proprietatea trecerii automate în timpul producției de produse dintr-o gamă arbitrară sau prestării de servicii de producție. Ele fac posibilă eliminarea aproape completă a muncii manuale în timpul operațiunilor de încărcare, descărcare și depozitare de transport și de a face tranziția la tehnologia cu aglomerație redusă.
o o o Sistemele de producție și logistică au următoarele proprietăți: Flexibilitatea sistemului de mașini (flexibilitatea echipamentelor) Flexibilitatea sortimentelor Flexibilitatea tehnologică Flexibilitatea volumelor de producție Flexibilitatea extinderii sistemului Versatilitatea sistemului se caracterizează printr-o varietate de piese (produse semifabricate) care pot fi procesate în sisteme flexibile de producție și logistică
Flexibilitatea sistemului de mașini (flexibilitatea echipamentelor). Acesta reflectă durata și costul tranziției către producția următorului articol de piese (produse semifabricate) în intervalul atribuit PLS flexibil. Un indicator al acestei flexibilități este considerat a fi numărul de piese fabricate în intervalele dintre ajustări. Flexibilitatea sortimentului. Acesta reflectă capacitatea PLC de a actualiza produsele. Principalele sale caracteristici sunt timpul și costul pregătirii producției unui nou tip de piese (produse semifabricate) sau a unui nou set de operațiuni logistice. Un indicator al flexibilității sortimentelor este coeficientul maxim de reînnoire a produsului sau complexul de operațiuni logistice, la care funcționarea sistemului PLC rămâne rentabilă. Flexibilitate tehnologică. Aceasta este flexibilitatea structurală și organizațională, care reflectă capacitatea PLC-ului de a utiliza diferite opțiuni de proces pentru a elimina posibilele abateri de la programul de producție pre-dezvoltat. Flexibilitatea volumelor de producție. Se manifestă prin capacitatea PLS de a produce rațional piese (produse semifabricate) în condiții de dimensiuni dinamice ale loturilor de lansare. Principalul indicator al flexibilității volumelor de producție este dimensiunea minimă a lotului (fluxurile de materiale) la care funcționarea acestui sistem rămâne rentabilă. Flexibilitatea extinderii sistemului. În caz contrar, se numește flexibilitatea de proiectare a PLS. Ea reflectă posibilitățile de modulare a acestui sistem și dezvoltarea (extinderea) ulterioară a acestuia. Cu ajutorul flexibilității de proiectare, se realizează posibilitățile de a combina mai multe subsisteme într-un singur complex. Un indicator al flexibilității proiectării este numărul maxim de echipamente care pot fi utilizate într-un PLS flexibil, menținând în același timp soluțiile de bază de proiectare pentru sistemul logistic (transport și depozit) și sistemul de management. Versatilitatea sistemului. Acest tip Flexibilitatea este caracterizată de o varietate de piese (produse semifabricate) care pot fi procesate în PLS flexibil. O evaluare a versatilității sistemului este numărul prevăzut de modificări ale pieselor (produse semifabricate) care vor fi procesate într-un PLS flexibil pe întreaga perioadă de funcționare.
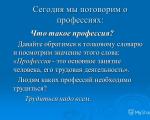